2005 - Volume #29, Issue #4, Page #43
[ Sample Stories From This Issue | List of All Stories In This Issue | Print this story
| Read this issue]
Self-Propelled TMR Mixer
![]() |
Mullenbach started with a new 375 cu. ft. Patz TMR mixer. Because it was needed morning and night to mix feed, work time on the add-on power unit was limited to mid day hours. That worked OK because Mullenbach intended to build it so it could be converted back to its tractor-tow configuration.
"I can convert it back to a tractor-towed unit in 20 minutes if I ever have a problem with the engine or other components on the power unit," says Mullenbach. "I just take six bolts out, lift the power unit out of the way, bolt the original hitch up and drive away."
He replaced the mixer's original axle with a hydraulic-powered truck axle. In its tow mode, the axle free-wheels.
Building the front end was trickier. Because it could not be integrated with the mixer's chassis until the last moment, Mullenbach built it so he can move it around with a forklift. This allowed him to move it into place on the mixer when needed.
"It was easier than using overhead hoists or blocks," says Mullenbach. "I can use the forklift to remove the power unit if I need to switch back to tow mode."
The power unit itself consists of an engine and hydrostatic drive from an IH 815 combine mounted on a frame built of 2 by 12-in. steel tubing. The operator area, without enclosure and front axle as well as the tin for enclosing the drive unit, came from a White 8700 combine. Originally, he had planned to use its motor and hydrostatics as well but that would have required mounting a separate hydrostatic drive unit with a drive belt.
"I ran across the IH 815 with the hydrostatic drive already mounted," explains Mullenbach. "It made the job super easy."
Integrating the chassis of the trailer with the chassis of the power unit was key to the project's success. The Patz hitch is designed to be adjusted to fit various height tool bars. Removing the hitch left a faceplate with six holes. The trailer frame angled to a point at the faceplate. Mullenbach designed his power unit frame with a plate that would bolt to the trailer hitch. The power unit frame also extended behind the plate to fit against the top of the trailer frame. Two posts extending down from the power unit frame, one on each side of the trailer frame, act as stabilizers.
Mullenbach mounted the engine so it faced the TMR trailer, leaving air space between the two. Tin mounted over the engine extends back and slightly over the trailer to block feed from spilling on the radiator.
Mounting the engine backwards allowed him to drop a belt from the main drive pulley to a 26-in. pulley mounted on the frame with a 540 pto shaft in line with the TMR pto. A hydraulic pump mounted in the IH gearbox provides power to raise, lower and run the unloading conveyer.
The open seat and controls mount high on the frame for visibility. "I wanted to see over the top of the mixer instead of using mirrors," says Mullenbach. "With no cab, I have to deal with the weather, but I have super visibility without having to wash windows."
He reports the unit works great on his concrete lot. He estimates out-of-pocket costs for the power unit and trailer adaptations ran him about $1,800.
If he were doing it over, Mullenbach says he would consider building an integrated power unit and chassis with combine drive wheels. Rather than unhooking the mixer trailer for tow-behind use, he would simply lift the mixer and wagon box off the new chassis and return it to the original chassis.
Contact: FARM SHOW Followup, Pat Mullenbach, 62562 130th St., Adams, Minn. 55908 (ph 507 582-3136)
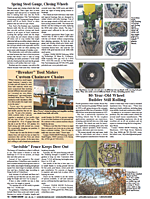
Click here to download page story appeared in.
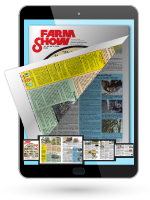
Click here to read entire issue
To read the rest of this story, download this issue below or click here to register with your account number.