Wagon Loads Bales Onto Pallets In The Field
When new retiree Ken Anselm put 25 acres back into hay production, he knew he was a one-man crew, so he built a bale wagon to do the job. Not only does it pick up bales, it sorts them into alternating positions so each layer “ties” to the previous layer. What’s more, the wagon stacks the 6-bale layers against a pallet. Once the pallet has 4 or 5 layers against it, the bale wagon tilts the pallet and bales 90 degrees and sets the loaded pallet on a trailer.
“When I was a senior in high school, I purchased a ’49 Ford flatbed truck, and some of my buddies and I followed a baler around all summer,” says Anselm. “We had a lot of fun and made good money. However, these days there is no way you can get kids to help hay. I decided if I was going to produce small square bales for the horse market, I would have to make it a one-man job.”
Anselm saw various systems for larger scale hay producers, but they would have required large investments and a larger tractor. He knew his 30 hp. New Holland 1620 couldn’t handle a grapple full of bales.
A broken leg and 6 months forced recuperation gave him time to plan an alternative. By the time he was back on his feet, the plans were complete. They called for an all-hydraulic wagon, 86 in. wide and about 24 ft. long. He calls it his Hayday machine.
A programmable logic controller (PLC) is key to the machine’s operation. It is connected to sensors that provide it with information that activates various electric- over-hydraulic controls. This allows Anselm to concentrate for the most part on steering the tractor while the Hayday Machine does the work.
The machine consists of 4 parts. The first is a pickup conveyer that swings out from between the wagon and the tractor. A hydraulic motor drives pickup chains that grab bales and deliver them to the sorting platform. As bales arrive on the sorting platform, multiple arms operated by hydraulic cylinders push successive bales into 6 preset positions on the loading platform. Once all 6 bales are in place, 2 cylinders tip the loading platform to a vertical position, depositing the bales against a 4 1/2 by 6-ft. pallet.
While a bale is being sorted or the platform is moving, the pickup conveyor stops. When the sorting platform drops back into place, bale pickup resumes. If the platform has emptied, new bales are sorted into a different configuration.
The pallet with its layer of bales sits at about a 10-degree angle against the forks of a forklift mast installed on its back at the rear of the HayDay Machine. A series of slats extend across the face of the mast, supporting the bottom edge of the bale layer.
“When the first layer of bales is pushed into place, the forks are near what would be the top of the mast,” explains Anselm. “As each successive layer is pushed into place, the forks move down the mast, and the slats move with them.”
When the desired numbers of layers are in place, a large cylinder tips the forklift mast upright. This puts the forks and pallet in a horizontal position. At that point they can be placed on the wagon for transport to storage.
“I can select either 4 or 5 layers per pallet in the PLC programming and do a manual override of the PLC to move the tongue or pickup left or right,” says Anselm. “Otherwise, the PLC controls the cylinders and the order of activation. Sorting alone requires as many as 5 cylinders to turn a bale a certain way.”
While there are a total of 14 cylinders and a hydraulic motor, the small tractor has plenty of power. No more than 2 cylinders are ever in action at any one time. While electronic and hydraulic components were new, many other components were repurposed.
“My 93-year-old dad Bernard is a big fan of FARM SHOW and has always made tools and any contraption he needed out of his scrap piles,” says Anselm. “He taught us kids to make do and not be afraid of tackling anything. That’s how I was raised.”
While he didn’t have scrap for everything he needed, Anselm did use the axle, wheels and some tubing from an old Allis Chalmers planter. The forklift mast was salvaged from a Hyster 50.
Anselm stacks 4 layers on his homemade pallets if storing them 2 high in his barn. He bought an old forklift for that part of the job. He stacks layers 5 high if they will be delivered to a customer. The system works well, he says.
“I only bale about 2,500 bales a year, and with the HayDay Machine, I can pick up as many as 500 bales a day,” says Anselm. He figures he has about $45,000 invested in the machine, close to half of it just in the hydraulics. While a grandson did much of the welding for him, Anselm designed and installed the hydraulics and electronics as well as programming the PLC.
“I used to work in manufacturing and we built machines using controllers of various types. I also had experience developing programs for PLCs,” says Anselm.
Contact: FARM SHOW Followup, Ken Anselm, P.O. Box 187, Le Center, Ky. 42056 (ph 270 519-1010; Ken@sistersandfriends.net).
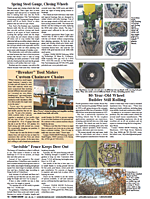
Click here to download page story appeared in.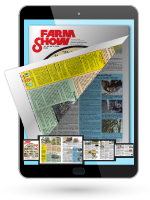
Click here to read entire issue
Wagon Loads Bales Onto Pallets In The Field BALE HANDLING When new retiree Ken Anselm put 25 acres back into hay production he knew he was a one-man crew so he built a bale wagon to do the job Not only does it pick up bales it sorts them into alternating positions so each layer “ties” to the previous layer What’s more the wagon stacks the 6-bale layers against a pallet Once the pallet has 4 or 5 layers against it the bale wagon tilts the pallet and bales 90 degrees and sets the loaded pallet on a trailer “When I was a senior in high school I purchased a ’49 Ford flatbed truck and some of my buddies and I followed a baler around all summer ” says Anselm “We had a lot of fun and made good money However these days there is no way you can get kids to help hay I decided if I was going to produce small square bales for the horse market I would have to make it a one-man job ” Anselm saw various systems for larger scale hay producers but they would have required large investments and a larger tractor He knew his 30 hp New Holland 1620 couldn’t handle a grapple full of bales A broken leg and 6 months forced recuperation gave him time to plan an alternative By the time he was back on his feet the plans were complete They called for an all-hydraulic wagon 86 in wide and about 24 ft long He calls it his Hayday machine A programmable logic controller PLC is key to the machine’s operation It is connected to sensors that provide it with information that activates various electric- over-hydraulic controls This allows Anselm to concentrate for the most part on steering the tractor while the Hayday Machine does the work The machine consists of 4 parts The first is a pickup conveyer that swings out from between the wagon and the tractor A hydraulic motor drives pickup chains that grab bales and deliver them to the sorting platform As bales arrive on the sorting platform multiple arms operated by hydraulic cylinders push successive bales into 6 preset positions on the loading platform Once all 6 bales are in place 2 cylinders tip the loading platform to a vertical position depositing the bales against a 4 1/2 by 6-ft pallet While a bale is being sorted or the platform is moving the pickup conveyor stops When the sorting platform drops back into place bale pickup resumes If the platform has emptied new bales are sorted into a different configuration The pallet with its layer of bales sits at about a 10-degree angle against the forks of a forklift mast installed on its back at the rear of the HayDay Machine A series of slats extend across the face of the mast supporting the bottom edge of the bale layer “When the first layer of bales is pushed into place the forks are near what would be the top of the mast ” explains Anselm “As each successive layer is pushed into place the forks move down the mast and the slats move with them ” When the desired numbers of layers are in place a large cylinder tips the forklift mast upright This puts the forks and pallet in a horizontal position At that point they can be placed on the wagon for transport to storage “I can select either 4 or 5 layers per pallet in the PLC programming and do a manual override of the PLC to move the tongue or pickup left or right ” says Anselm “Otherwise the PLC controls the cylinders and the order of activation Sorting alone requires as many as 5 cylinders to turn a bale a certain way ” While there are a total of 14 cylinders and a hydraulic motor the small tractor has plenty of power No more than 2 cylinders are ever in action at any one time While electronic and hydraulic components were new many other components were repurposed “My 93-year-old dad Bernard is a big fan of FARM SHOW and has always made tools and any contraption he needed out of his scrap piles ” says Anselm “He taught us kids to make do and not be afraid of tackling anything That’s how I was raised ” While he didn’t have scrap for everything he needed Anselm did use the axle wheels and some tubing from an old Allis Chalmers planter The forklift mast was salvaged from a Hyster 50 Anselm stacks 4 layers on his homemade pallets if storing them 2 high in his barn He bought an old forklift for that part of the job He stacks layers 5 high if they will be delivered to a customer The system works well he says “I only bale about 2 500 bales a year and with the HayDay Machine I can pick up as many as 500 bales a day ” says Anselm He figures he has about $45 000 invested in the machine close to half of it just in the hydraulics While a grandson did much of the welding for him Anselm designed and installed the hydraulics and electronics as well as programming the PLC “I used to work in manufacturing and we built machines using controllers of various types I also had experience developing programs for PLCs ” says Anselm Contact: FARM SHOW Followup Ken Anselm P O Box 187 Le Center Ky 42056 ph 270 519-1010; Ken@sistersandfriends net
To read the rest of this story, download this issue below or click
here to register with your account number.