You have reached your limit of 3 free stories. A story preview is shown instead.
To view more stories
(If your subscription is current,
click here to Login or Register.)
Home-Built Chop Saw "Made To Last"
“I couldn’t find a metal cutting abrasive chop saw with an electric motor that wouldn’t burn up within 12 months, so I built my own using a motor with a thermal switch to prevent overheating. It’s built to last,” says John Betka, Walkerville, Mont.
He used salvaged parts from a pair of Milwaukee chop saws,
..........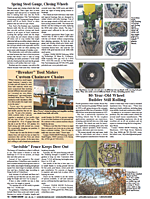
You must sign in, subscribe or renew to see the page.
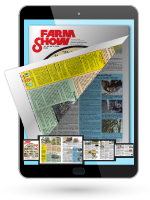
You must sign in, subscribe or renew to see the flip-book
Home-Built Chop Saw Made To Last FARM SHOP Miscellaneous “I couldn’t find a metal cutting abrasive chop saw with an electric motor that wouldn’t burn up within 12 months so I built my own using a motor with a thermal switch to prevent overheating It’s built to last ” says John Betka Walkerville Mont He used salvaged parts from a pair of Milwaukee chop saws including the handle blade guard switch and tilt pivot pin and spring The rest of the chop saw was made from scrap steel remnants that he already had The unit is chain-driven using two 2-in dia sprockets and a no 40 chain “I built it last fall and so far it has cut anything I put under it without any strain on the motor at all ” says Betka The chop saw is operated by a 1 1/2 hp Marathon electric motor equipped with a thermal protection switch to prevent overheating He bought the motor from Surplus Center in Lincoln Neb www surpluscenter com; ph 800 488-3407 It was designed to run on 240-volt AC and run at 3 450 rpm’s which would have made the blade go too fast So he installed a large sprocket on the motor and a smaller sprocket on the blade’s driveshaft which slowed the motor down to 1 800 rpm’s The 1 1/2 hp motor was designed to operate on either 110 or 240-volt AC but didn’t have enough torque to turn the blade adequately so he replaced the capacitor with a larger one made for a 240-volt motor He also replaced the capacitor’s cover “I couldn’t find a cover that was the right size so I made one out of a 1 3/4-in piece of schedule 40 pvc pipe and screwed it onto the motor ” says Betka “One side of the cover comes off so if I need to I can easily replace the capacitor ” He wasn’t happy with the performance of the original abrasive blade on the Milwaukee chop saw or with any other abrasive blades that he had tried before because they wore out too fast Then he discovered Flexovit abrasive blades Eagle Safety Products Union Mo www eaglesafetyproducts com; ph 636 583-4428 “I first tested out a used 24-in dia Flexovit blade that I got from a local steel supplier The blade was worn down too much for them to use anymore but it worked great for me and lasted a long time So I ordered 14-in dia replacement blades from the company The blades are 1/4 in thick and are made with some kind of compressed grit with a bonding agent I’ve found they last much longer than anything else on the market ” He made one more improvement to his home-built saw The Milwaukee chop saw’s deck originally measured only 10 by 14 in which he found too small so he installed a 24-in sq 1/4-in thick steel plate on top of it to provide more room when cutting material “It’s ugly but it works great ” says Betka “I spent about $135 for the motor and blade whereas comparable new chop saws sell for $200 and up Also all the parts on my chop saw are standard parts that I can buy at any farm and ranch store With Milwaukee chop saws you can’t buy a replacement motor armature or field separately and a lot of their other replacement parts are discontinued after 2 years ” Betka says he’s had a lot of problems with all the current brands of chop saws including the Milwaukee “I don’t know if the manufacturers have lowered their specifications or if it’s just a matter of poor quality materials But I’ve had the motors burn out within 12 months on 2 handheld grinders 2 chop saws and 3 drills It doesn’t seem to matter if I upgrade to a company’s heavy duty models or not ” Contact: FARM SHOW Followup John Betka 5889 Moulton Reservoir Road Walkerville Mont 59701 ph 406 490-2980; jcb@crbart com
To read the rest of this story, download this issue below or click
here to register with your account number.