You have reached your limit of 3 free stories. A story preview is shown instead.
To view more stories
(If your subscription is current,
click here to Login or Register.)
Small Engine Stand Makes Repairs Easy
Jerry Maddock didn’t want to bend over his Briggs & Stratton engines as he worked on them. So he built a stand that lets him work from a chair and rotate the engine as needed. It also serves as a handy mount for his innovative flywheel holder.
“I wanted to be able to roll up in a chair and be able to move th
..........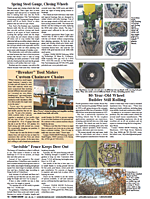
You must sign in, subscribe or renew to see the page.
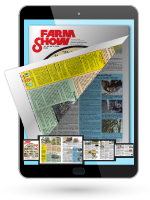
You must sign in, subscribe or renew to see the flip-book
Small Engine Stand Makes Repairs Easy ENGINES Jerry Maddock didn’t want to bend over his Briggs & Stratton engines as he worked on them So he built a stand that lets him work from a chair and rotate the engine as needed It also serves as a handy mount for his innovative flywheel holder “I wanted to be able to roll up in a chair and be able to move the engine around the shop as I worked on it ” says Maddock “It lets me take apart an engine work on it and reassemble it without ever taking it off the stand ” He started with a commercial H-frame engine stand with an engine support arm He modified the base and the mounting plate He cut off all 4 wheels and replaced them with the locking castors They ensure the stand remains in place even if it tips so 2 wheels come off the floor The original stand allowed the mounting arm and engine to be rotated into one of several fixed positions Maddock wanted infinite positions but commercial stands with that option cost several hundred dollars The original system involved a round steel shaft that extended through a housing on the stand’s upright and attached to the engine support arm mounting plate A bar at the rear was turned to rotate the engine into positions at 45° intervals Maddock replaced the bar with a salvaged worm gear drive from a winch I removed the cable from the winch and attached it to a round ring that I milled to fit over the mounting plate shaft says Maddock The worm drive lets me easily rotate the mounting plate and engine I use two set screws and a pin to lock the shaft in place On these light engines I can pull the set screws and pin slide the winch off and free wheel the engine Since the bulk of the engines he works on are small Briggs & Stratton s Maddock made a bracket specific for these engines and bolted it in place of the support arm It bolts to the engines where their starter/generator would normally attach Other brackets work with larger engines If he needs to work on a flywheel he makes special brackets with a curve for the flywheel He uses a pipe bender on a piece of steel strap to match the curve of the flywheel A tab on the end of the curve fits over a fin on the flywheel Once the bracket is in place Maddock adds more tabs to “sandwich” multiple fins When you’re trying to torque a flywheel off or on it wants to lift constantly and you need someone to hold the engine down says Maddock With this I can torque the flywheel myself Maddock has also fabricated a front engine support for his Simplicity garden tractor It bolts to the mounting plate It lets me rotate the front end for welding new bearings in place and other work says Maddock Whether front end or engine the worm gear lets me adjust them as little or as much as I want Contact: FARM SHOW Followup Jerry Maddock 29197 Standley Rd Defiance Ohio 43512 ph 419 395-1594; jmachine@ayersvilletelco com
To read the rest of this story, download this issue below or click
here to register with your account number.