1980 - Volume #4, Issue #2, Page #04
[ Sample Stories From This Issue | List of All Stories In This Issue | Print this story
| Read this issue]
Research Breakthrough For Farm Alcohol Stills
A new process developed by Iowa State University researchers produces grain alcohol faster, cheaper and with less energy than the conventional distillation process incorporated into most on-farm stills now being sold commercially.The new process absorbs alcohol from the fermentation beer, rather than using distillation and drying processes to manufacture alcohol, reports Colin Chriswell, associate chemist with Ames Laboratory, Department of Energy, Iowa State University, Ames, Iowa. "This new process is efficient and has high alcohol production capacity," he told FARM SHOW.
Chriswell explains that in typical on-farm stills, or similar alcohol production systems, fermenter beer of about 9% alcohol content is run through a distillery to concentrate the alcohol to about 95%. Next, a drying process concentrates the alcohol to 200 proof, or pure alcohol.
Chriswell feels the new absorption method has several advantages over drying the distilled product to remove alcohol.
1. A major concern about on-farm alcohol production has been the large amount of energy needed in the distillation and drying process. This new absorption process uses considerably less energy to produce 200 proof alcohol.
2. Equipment used in the new absorption process is very simple, cornpared with distillation equipment.
3. Chriswell says the absorption process can remove alcohol from the beer as the fermentation process is going on, permitting continuous alcohol production. In current distilation processes, the fermentation system must be closed down to be emptied and refilled.
4. In the conventional still's fermentation-distillation process, yeasts that produce the beer are killed when the alcohol content reaches about 14%. The yeasts slow down and are less efficient, at even lower alcohol contents. With the absorption process, yeasts can remain viable because the alcohol is removed before
the yeasts become inefficient.
Will the new process make justintroduced commercial on-farm alcohol stills obsolete?
"Not in the near future," answers Chriswell. He predicts that "a moderate size prototype production unit, with production capacity of 5,000 to 10,000 gals. per year of 200 proof alcohol, could be in operation within one year. Our current rate of research could perfect the absorption process for commercial operation within 3 to 5 years.
For more details, contact: FARM SHOW Followup, Colin Chriswell, Associate Chemist, Ames Laboratory, Department of Energy, Ames, Iowa 50010.
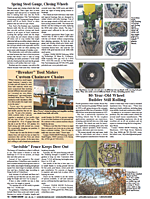
Click here to download page story appeared in.
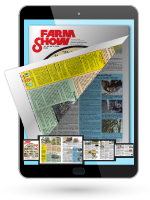
Click here to read entire issue
To read the rest of this story, download this issue below or click here to register with your account number.