You have reached your limit of 3 free stories. A story preview is shown instead.
To view more stories
(If your subscription is current,
click here to Login or Register.)
How To Make A Simple Biodiesel Processor
If you're looking for an inexpensive way to make biodiesel, and you've got some time on your hands, you might be interested in how Ron Carey got started.
He built a simple processor, nicknamed the "Bedrock Brewer", to make biodiesel for about 60 cents per gal.
Because he uses the sun to heat his vegetable
..........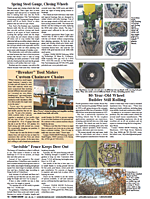
You must sign in, subscribe or renew to see the page.
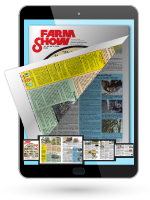
You must sign in, subscribe or renew to see the flip-book
How To Make A Simple Biodiesel Processor ENERGY Alternative Fuels 30-4-34 If you're looking for an inexpensive way to make biodiesel, and you've got some time on your hands, you might be interested in how Ron Carey got started.
He built a simple processor, nicknamed the "Bedrock Brewer", to make biodiesel for about 60 cents per gal.
Because he uses the sun to heat his vegetable oil before processing, Carey admits that it can take awhile to get the oil hot enough to process.
Carey built the processor from a steel 55-gal. barrel, an inexpensive pump he bought from Harbor Freight (www.harborfreight.com; ph 800 444-3353), black steel pipe, and brass valves. He says he probably spent about $150 on it.
He removed the bungs from the barrel and painted it black so it absorbs heat. He attached black steel piping and brass valves to each bung hole. One drains the byproduct glycerol and the other is used to pull liquid from the bottom of the barrel using the pump.
He elevated the processor 2 ft. off the ground on a platform made from concrete blocks and wood. The pump mounts under the platform.
Before processing the used vegetable oil that restaurants give him, Carey lets the containers sit in the sun. On a hot and sunny summer day, it takes a couple of hours to heat the oil. "Ideally, oil temp needs to be 130 degrees or so to get a good reaction," he says. "Many biodiesel ębrewers' use a water heater as a reaction vessel so water elements heat the oil faster," he says.
After it's hot enough, he pours the oil into the barrel. He can process 45 gal. of oil at a time.
Then he does a titration test to determine the Free Fatty Acid (FFA) content. "It's a simple chemical test. Any fourth grader can do it." The results are then plugged into a simple math test. The more used the oil is, the higher the FFA.
The test determines how much lye and potassium hydroxide or sodium hydroxide to add to methanol to create the methoxide that he adds to the oil. For 45 gal. of oil, he might add 9 gal. of methoxide.
He's adamant about safety while combining these chemicals. He wears goggles, gloves and protective clothing.
After adding the methoxide, he lets the processor mix for about an hour. Then it sits for 8 hours to let the glycerol separate from the biodiesel. There's about 9 gal. of it that gets siphoned off. Carey hasn't found a use for the glycerin although he knows it's used to make soap.
Lastly, Carey pours the biodiesel into separate containers and lets it sit for about two weeks to separate the impurities from the biodiesel before using it in his diesel vehicles.
"It's not as complicated as one might think, and the first few times are the hardest," he says. "With a little ingenuity, some investment and willingness to learn, it's worth the time and effort."
Carey is the "production master" of the Yoderville BioDiesel Club. They've "brewed" over 5,000 gal. of biodiesel.
Contact: FARM SHOW Followup, Ron Carey, 205 Cedar St., West Chester, Iowa 52359 (ph 319 698-2341; burlman69 @ yahoo.com; www.ydbc.org).
To read the rest of this story, download this issue below or click
here to register with your account number.