1992 - Volume #16, Issue #3, Page #04
[ Sample Stories From This Issue | List of All Stories In This Issue | Print this story
| Read this issue]
Simple Guidance System
"It sells for less than half the price of other guidance systems and outperforms them all," says Eugene Anderson, Nevada, Mo., about the uncomplicated new guidance system he developed for use on his own farm after being dissatisfied with a commercial system he purchased."It surprised us by working much better than we ever thought it would. It does what other systems said they would do but never did - lets you operate the tractor without having to think about it," says Anderson, who's already sold 60 of the units, along with partner Gary Balk, and is currently negotiating with a major manufacturer who plans to put the system on the market nationwide.
The biggest problems with conventional guidance systems, says Anderson, are too many electronic controls and the fact that they move the hitch point back 4 to 6 in. from the tractor.
Anderson's system is simple. It consists of a channel iron bracket that slips over the drawbar and pins in place. It supports a double-acting 8-in. stroke hydraulic cylinder that mounts between the drawbar bracket and one side of the 3-pt. Row sensing fingers, mounted below the tractor, sense the location of the row and send signals to a "mechanical" control box mounted on top of the 3-pt. The control box works off mechanically-triggered micro-switches because Anderson says they're much simpler and easier to work on if anything goes wrong.
"These units contain no circuit boards or computers. Virtually every part is available off-the-shelf with the exception of the valves, which are made in Kansas City, Mo. Total weight of the system is less than 100 lbs. and it can be used with or without a quick hitch. Mounts easily with two bolts, two hydraulic connections and one electric plug. Doesn't interfere with shields or other equipment on toolbar and works with open or closed hydraulics," says Anderson.
Rather than shift the toolbar back and forth constantly like other systems, the new AB Guidance System shifts the tractor rear end back and forth. "It corrects in less than 3 ft. at normal field speeds. The sensors have 1 in. tolerance to prevent constant corrections. The effect in the field is that the toolbar runs straight with the rows while the tractor rear end shifts constantly. Mean-while, the control cylinder compensates and then relaxes when the correct position is reached. There's no pressure on the cylinder unless it's making a correction.
"One key feature is that this system self-centers when you raise it at the end of the field. Getting back on the row has been a major problem with some other guidance systems. Total range of correction is about 11 in. or 51/2 in. to either side. Whenever corrections are being made, an indicator light in a control box in the cab signals the operator which direction to steer to correct, which is a real aid on terraces or curved rows."
Anderson says he's field-tested the unit on 12-row cultivators over thousands of acres in all kinds of crops and conditions with near perfect results. "It's been nearly trouble-free and in 10 years it'll still be working because there's little to wear out. Works particularly well on terraces and hillsides. We feel it's the next step forward in guidance systems. Can also be used on sprayers and we plan to adapt it to planters and drills."
At a price of less than $2,000, the new AB system costs less than half of many other systems.
Contact: FARM SHOW Followup, AB Company, Rt. 3, Box 457, Nevada, Mo. 64772 (ph 417 398-2636).
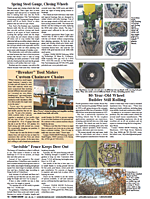
Click here to download page story appeared in.
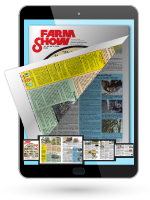
Click here to read entire issue
To read the rest of this story, download this issue below or click here to register with your account number.