Sprouting Oats Seal Big Bale Silage
 ✖  |
Dallas DeWitt, and his neighbor Ray Fausak, Wildwood, Alberta, began experimenting with big bale silage nearly 5 years ago under a Canadian government grant. After trying just about every possible storage method, they've now come up with a procedure - which including the use of sprouting oats as a sealer - they say makes silage at the lowest possible cost with the highest possible efficiency.
"Our main reason for making bale silage is our long rainy season. We don't have to wait for good weather anymore," says DeWitt. "I feel that we get about 50% more feed value, compared with ordinary hay bales. We have virtually no leaf loss, quality is nearly identical to stored silage, protein content is much higher and cows eat everything. There's nothing left in the bottom of the feeder when they get through."
The men first tried storing bales in individual plastic bags but said that more than 50% of the bags broke open. They tried storing bales in long plastic bags and found that, while the plastic held up better, the $3 to $4 per bale cost of the plastic was prohibitive. Then they tried stacking bales above ground and covering them. This worked better and the cost of plastic, at $1.50 per bale, was lower. However, they found it hard to seal off leaks to eliminate spoilage.
"Finally, after five years of experimentation, we began storing bales in a pit and found that this is by far the best method," DeWitt told FARM SHOW. "Feed quality is excellent, it's easy to seal off, and plastic costs just 70 cents per bale."
The pit used is 30-ft. wide at the bottom and 35-ft. across at the top. It's 12 ft. deep and 90 ft. long. The men placed 225 bales about 4.5-ft. dia. in the pit with each bale weighing about 2,000 lbs. They pack the stack with a 4-WD tractor and cover it with one layer of 6 mil plastic and seal the edges with sand. Chopped straw covers the plastic and then 5 gal. of oats are sprinkled over the straw. The oats sprout and form a green protective mat over the plastic.
"We've had virtually no spoilage with this method. We open it up from one end to remove bales and then reseal it," says DeWitt, noting that the sides of the pit are also lined with plastic and the bottom covered with coarse gravel for good drainage.
DeWitt and Fausak recommend baling at between 65% and 55% moisture. They say you should never bale at more than 70% or under 50%, and point out that a moisture tester is a must. They recommend staying within manufacturers recommended bale weight. DeWitt has used the same New Holland 851 baler to make more than 1,000 high-moisture bales and says it's ideal, along with Deere's 530 baler. "You have to have a dense core baler. Soft core bales will spoil in the pit," he says.
Silage bales should be covered the same day they're made so usually two men are required ù one to operate the baler and another to haul them back to the pit. DeWitt and Fausak say they have been able to bale and cover as many as 200 bales per day.
For more information, and an in-depth report on making round bale silage, send $1.00 for postage to: FARM SHOW Followup, West Central Forage Association, Box 360, Evansburg, Alberta T0E 0T0.
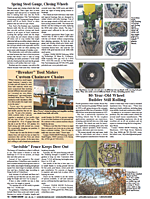
Click here to download page story appeared in.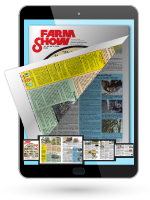
Click here to read entire issue
Sprouting oats seal big bale silage CROPS New Techniques 9-3-29 Dallas DeWitt, and his neighbor Ray Fausak, Wildwood, Alberta, began experimenting with big bale silage nearly 5 years ago under a Canadian government grant. After trying just about every possible storage method, they've now come up with a procedure ù which including the use of sprouting oats as a sealer ù they say makes silage at the lowest possible cost with the highest possible efficiency.
"Our main reason for making bale silage is our long rainy season. We don't have to wait for good weather anymore," says DeWitt. "I feel that we get about 50% more feed value, compared with ordinary hay bales. We have virtually no leaf loss, quality is nearly identical to stored silage, protein content is much higher and cows eat everything. There's nothing left in the bottom of the feeder when they get through."
The men first tried storing bales in individual plastic bags but said that more than 50% of the bags broke open. They tried storing bales in long plastic bags and found that, while the plastic held up better, the $3 to $4 per bale cost of the plastic was prohibitive. Then they tried stacking bales above ground and covering them. This worked better and the cost of plastic, at $1.50 per bale, was lower. However, they found it hard to seal off leaks to eliminate spoilage.
"Finally, after five years of experimentation, we began storing bales in a pit and found that this is by far the best method," DeWitt told FARM SHOW. "Feed quality is excellent, it's easy to seal off, and plastic costs just 70 cents per bale."
The pit used is 30-ft. wide at the bottom and 35-ft. across at the top. It's 12 ft. deep and 90 ft. long. The men placed 225 bales about 4.5-ft. dia. in the pit with each bale weighing about 2,000 lbs. They pack the stack with a 4-WD tractor and cover it with one layer of 6 mil plastic and seal the edges with sand. Chopped straw covers the plastic and then 5 gal. of oats are sprinkled over the straw. The oats sprout and form a green protective mat over the plastic.
"We've had virtually no spoilage with this method. We open it up from one end to remove bales and then reseal it," says DeWitt, noting that the sides of the pit are also lined with plastic and the bottom covered with coarse gravel for good drainage.
DeWitt and Fausak recommend baling at between 65% and 55% moisture. They say you should never bale at more than 70% or under 50%, and point out that a moisture tester is a must. They recommend staying within manufacturers recommended bale weight. DeWitt has used the same New Holland 851 baler to make more than 1,000 high-moisture bales and says it's ideal, along with Deere's 530 baler. "You have to have a dense core baler. Soft core bales will spoil in the pit," he says.
Silage bales should be covered the same day they're made so usually two men are required ù one to operate the baler and another to haul them back to the pit. DeWitt and Fausak say they have been able to bale and cover as many as 200 bales per day.
For more information, and an in-depth report on making round bale silage, send $1.00 for postage to: FARM SHOW Followup, West Central Forage Association, Box 360, Evansburg, Alberta TOE OTO.
To read the rest of this story, download this issue below or click
here to register with your account number.