You have reached your limit of 3 free stories. A story preview is shown instead.
To view more stories
(If your subscription is current,
click here to Login or Register.)
Self-Loading Feed Mixer Built From Old Combine
After looking at commercially-built self-loading feed mixer trucks and deciding that he could not justify the price, Kim Moon, Melba, Idaho, built his own self-loading mixer-feeder.
It loads itself and automatically weighs and mixes feed ingredients into a precise total mixed ration. In fact, Moon's home-built ri
..........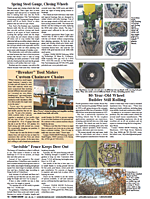
You must sign in, subscribe or renew to see the page.
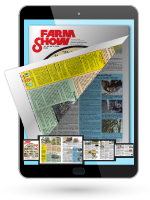
You must sign in, subscribe or renew to see the flip-book
Self-Loading Feed Mixer Built From Old Combine COMBINES Conversions 20-5-40 After looking at commercially-built self-loading feed mixer trucks and deciding that he could not justify the price, Kim Moon, Melba, Idaho, built his own self-loading mixer-feeder.
It loads itself and automatically weighs and mixes feed ingredients into a precise total mixed ration. In fact, Moon's home-built rig worked so well he has started custom-building the self-propelled rigs for other farmers and ranchers.
"It works as well as any commercial model but we can sell it for about $70,000, half the price of some commercial units," says Moon.
The innovative feed truck is equipped with a 23-in. wide front loader conveyor that loads silage, hay and other crops, as well as grain and protein concentrate. It conveys feed to a 16-ft. long, 6-ft. high box equipped with 4 mixer augers and electronic scales. Two digital monitors, one located in the cab and the other outside the cab, allow the operator to control ingoing and outgoing feed weights and quantities. Moon bought the mixer box from Kirby Mfg. (P.O. Box 989, Merced, Calif. 95341 ph 209 723-3941), but built the rest of the machine on his own using the frame, cab, engine, and front wheels off a 1977 International 915 combine.
Moon says the feed mixer truck can be used to load out corn silage from bunker silos and haylage from Ag Bags. It can also grind up and then load any size or shape hay bale. The header reaches up to 12 ft. high for silage pits.
He bought the combine from an implement dealer for $4,800 equipped with a 414 cu. in, 150 hp turbocharged diesel engine and a 3-speed hydrostatic transmission. He stripped it down to the frame, engine, and cab. He used 9-in. channel iron to build a new frame and made mounting brackets for the engine, cab, and box. He turned the frame around so that the steering axle is in front. He installed the cab on one side of the frame, then installed the radiator on the other side and mounted the engine behind it. The loading elevator is mounted between the cab and engine. He built it from sheet metal supported by steel tubing that supports a "high abrasive" steel floor. He used a length of 6-in. dia. steel pipe equipped with 5 1/2-in. flighting to build the auger.
"I reversed the combine's frame so it would be better able to support the weight of the box. On a combine most of the weight is on front whereas on a feed mixer truck most of the weight is on back," notes Moon.
He paid $27,000 for the box and mounted 23.1 by 26, 4-ft. high tires on back to support it. The combine's 16-in. steering wheels weren't built heavy enough to sup-port the front of the truck so he bought heavy duty split wheel rims and welded 3/16-in. thick steel plate inside the rims, then drilled out new holes for the bolts.
The combine's original hydraulic system raises and lowers the front loader auger and also operates the power steering. Moon installed a second hydraulic pump that operates the conveyor and four augers inside the box. The pump is belt-driven off the engine crankshaft. Two hydraulic cylinders are used to raise or lower the front loading auger, two cylinders are used to open the side discharge conveyor door, and another cylinder is used to open a flapper at the end of the conveyor. Another cylinder is used to swing a cab-mounted ladder back alongside the truck. "The ladder extends down to within 1 1/2 ft. of the ground which makes it easy to climb into the cab. In some feed-lots you have to drive very close to the bunks in order to dump feed into them and the lad-der could get ripped off if you're not careful. Commercial models have a ladder with only one step and you practically have to jump up to reach it."
Contact: FARM SHOW Followup, Kim H. Moon, 6840 Warren Spur Road, Melba, Idaho 83641 (ph 208 495-1268).
To read the rest of this story, download this issue below or click
here to register with your account number.