You have reached your limit of 3 free stories. A story preview is shown instead.
To view more stories
(If your subscription is current,
click here to Login or Register.)
Straw Bale Machine Shed Cost Just $4,000
Arlen and Marian Stocking built a 4,704 sq. ft. machine shed and they only spent about $4,000 to do so.
The walls of the shed are made of 110 big square straw bales and the roof was made out of a network of salvaged oil-field pipe covered with canvas.
"I expect these bales will probably outlast me," says
..........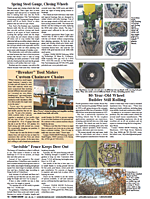
You must sign in, subscribe or renew to see the page.
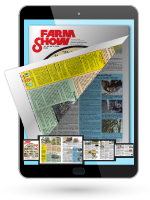
You must sign in, subscribe or renew to see the flip-book
Straw Bale Machine Shed Cost Just $4,000 CROPS Straw 17-4-10 Arlen and Marian Stocking built a 4,704 sq. ft. machine shed and they only spent about $4,000 to do so.
The walls of the shed are made of 110 big square straw bales and the roof was made out of a network of salvaged oil-field pipe covered with canvas.
"I expect these bales will probably outlast me," says Stocking, noting that his biggest concern after building the structure was that the bales would settle unevenly, but that hasn't been a problem. "The roof is a hay tarp that has been treated to withstand ultraviolet rays and has a life of 4 to 7 years. It cost me $1,500 and I'll be happy if I get 5 years out of it."
One big benefit of the bale building is the outstanding insulating value of the straw structure. Stocking says his trucks started much easier last winter. "The walls are basically 4 ft. of insulation and they're very effective at keeping wind out and warmth in."
Outer measurements of the shed are 105 by 56 ft. Inner measurements are 98 by 48 ft.
He used flax straw for the building because it's tough and fibrous so it weathers slowly. Before building the machine shed, he visited a farm with a straw hog barn and a machine shed made out of barley straw that was fitted with a permanent roof. He used some of the ideas he found there and added a few of his own. He put the building up himself over a period of two years, working when he had time, but says he's sure he could have put it up in about a week if he had had time. "It's not hard to build once you know what you're doing," he says.
He started with a rock base foundation which lets water drain away from the bales. A ditch runs alongside to help handle spring runoff. Bales are stacked 3-high to make 12-ft. walls. One end of the building is sealed shut. The other end is partially open. Five 25-ft. treated wood poles are spaced evenly down the center of the shed to support the roof peak, .which is a 10-in. pipe welded together in 40-ft. lengths.
"I cut holes in the bottom of the pipe so the support poles stick right up into the pipe. Every 10 ft., rafters come down from the peak to the bales," says Stocking. Hooks on the upper ends of the rafters hook into the peak pipe. He put forks on the lower end made out of 3/4-in. sucker rod that stick into the bale sides about 4 ft. He used a tractor loader to push forks down into bales. The center support poles are crossbraced with steel cable.
Stocking had the tarp custom-made. It has a sleeve around the edges so a pipe can be slipped inside for tie-downs. He punched holes in the sleeve every 30 ft. to attach tie-down cables to 3/4-in. anchor rods. A come-along winch is left in place on each cable to tighten the roof as needed. Nylon rope run in a zig zag pattern from the sleeve rod down to other rods which are stuck into the sides of the bales.
"Due to settling, I have had to tighten the tarp up periodically since the shed was completed," says Stocking.
The cost was about one-fifth the price of what he would have had to pay for a similar-size permanent building. "It's one of the best investments I've ever made," says Stocking. "I'm surprised there aren't more of these things around."
Contact: FARM SHOW Followup, Arlen Stocking, Rt. 2, Barrhead, Alberta TOG OEO Canada.
To read the rest of this story, download this issue below or click
here to register with your account number.