You have reached your limit of 3 free stories. A story preview is shown instead.
To view more stories
To view more stories
SUBSCRIBE OR RENEW NOW
(If your subscription is current, click here to Login or Register.)1996 - Volume #20, Issue #4, Page #40
[ Sample Stories From This Issue | List of All Stories In This Issue]
Universal Closing Wheels For Planters
"Our new planter closing wheels are de-signed to adapt to all conditions at planting, unlike other wheels that only work when conditions are near perfect," says inventor Walter Carroll, Wauneta, Neb., who's currently testing his innovative planter add-ons with Deere & Co. and Agco Allis-White.Five years ago Car..........
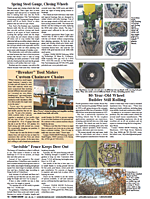
You must sign in, subscribe or renew to see the page.
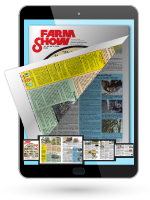
You must sign in, subscribe or renew to see the flip-book
Universal Closing Wheels For Planters PLANTING EQUIPMENT Accessories Our new planter closing wheels are de-signed to adapt to all conditions at planting unlike other wheels that only work when conditions are near perfect says inventor Walter Carroll Wauneta Neb who s currently testing his innovative planter add-ons with Deere & Co and Agco Allis-White Five years ago Carroll was the first to try using spoked wheels as closing wheels by mounting the specially-curved spoked wheels in place of the original closing wheels Vol 17 No 4 The spoked wheels pinch the furrow from the sides rather than shoving dry surface soil back over the seed The tilling action of the spoked wheels leaves the soil in a mulched condition above and to the sides of the seed He licensed his original patent to Acra Plant His new patent pending EquaMizer system uses spoked wheels that are partially covered by 11 1/2-in dia aluminum plates The plates cover one or both sides of the closing wheels depending on soil conditions The spoked wheels are 13 in in diameter so 1 1/4 in of each spoke extends beyond the aluminum cover plates The half-section plates are held on by metal clips and can be fastened to either the inside or out-side of the wheel You can tailor the system to any combination of tillage or soil moisture conditions says Carroll You can use it four different ways - closing wheels only double plates or single plates mounted inside or outside the closing wheels The spokes perforate the soil and the cover plates pack it down over the slot There s just enough spoke exposed to break up the soil When both plates are bolted together it s the widest closing wheel on the market Works great in low moisture conditions where you want to seal in all available moisture In some cases farmers will want the flotation provided by both plates However in no-till or tight soil you can use just the half sections which can penetrate heavy residue more easily without riding on top Also in wet soils that resist closing the half sections pack the soil tighter if that s what is desired Most planter manufacturers offer either rubber or cast iron closing wheels Each wheel works good in certain conditions However neither type of wheel works adequately in all conditions and a lot of farmers don t want to spend the money to own more than one set For example cast iron wheels are designed primarily for no-till and can t be used on soft ground because they re so narrow and heavy that they d bury them-selves in the soil Another problem is that switching from rubber to cast iron wheels or visa versa is a big job With my system you simply slide each plate over the axle that supports the closing wheel and rotate three clips - there s no need to remove the wheels or bearings In the near future farmers will be planting genetically altered seed Because of the high cost per acre of this seed farmers can t afford to plant without making sure that the seed is tucked properly into the soil I got the idea when I tried to develop a wider closing wheel for cotton farmers who were having problems with soil crusting over the seed resulting in poor seed emergence Many of them had to replant after heavy rains I found that the bolted-together plates and spoked wheel combination created depressions where rain allowed silt to settle Cracks developed between depressions encouraging cotton seed emergence In super heavy ground where you re concerned about closing the slot I recommend mounting half section plates inside the wheels so they can apply more pressure to the slot In heavy clay soil that s farmed no-till you don t have to worry about soil crusting over the slot so you can mount the plates on the outside The spokes will perforate soil from the inside and create a deeper depression so that it ll warm up quicker We found this worked really well in Illinois on heavy clay soil where the farmer planted into a cover crop of ryegrass Four molded circular “knobs” on one side of the plate fit between the spokes and are used to bolt the two half sections together The half section plates are made in left and right hand versions The left version goes on the outside of the left closing wheel and the right version goes on the outside of the right wheel If you want to cover just the inside of the wheels put the left hand plate on the inside of the right wheel and the right hand plate on the inside of the left wheel The cover plates are expected to sell for $60 per row Contact: FARM SHOW Followup Walter Ray Carroll HCR 65 Box 77 Wauneta Neb 69045 ph 308 394-5888
To read the rest of this story, download this issue below or click here to register with your account number.