You have reached your limit of 3 free stories. A story preview is shown instead.
To view more stories
(If your subscription is current,
click here to Login or Register.)
Snowplow Hay Windrower
Hay rakes are a common sight in Pennsylvania but no other rake looks anything like the one owned by Mark Pugliese. It uses a pair of curved steel blades equipped with powered spinning rollers on the bottom edge of each blade to gently lift hay off the stubble and "plow" it into windrows.
"It minimizes leaf loss,
..........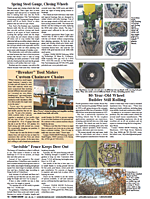
You must sign in, subscribe or renew to see the page.
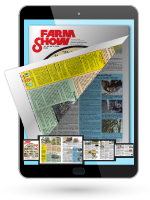
You must sign in, subscribe or renew to see the flip-book
Snowplow Hay Windrower HAY & FORAGE HARVESTING Miscellaneous 16-1-29 Hay rakes are a common sight in Pennsylvania but no other rake looks anything like the one owned by Mark Pugliese. It uses a pair of curved steel blades equipped with powered spinning rollers on the bottom edge of each blade to gently lift hay off the stubble and "plow" it into windrows.
"It minimizes leaf loss, boosting the nutritional value of harvested alfalfa," says Pugliese, who built the prototype windrower last summer.
The 12-ft. wide machine can be used to windrow swathed hay or to combine two windrows into one and can also be used as a hay inverter. It consists of two 2-ft. high, 41/2-ft. long stainless steel blades set 3 ft. apart and mounted at a 45 degree angle to the swath or windrow. The bottom of each blade is equipped with a spinning, 3 1/2-in. dia. fluted-steel roller powered by a ptodriven hydraulic pump. The rollers pick up the hay which then slides backward along the blades.
"My friends say it looks like I'm operating a high-speed snowplow because the rollers almost disappear from view in the hay stubble," says Pugliese, an ex-dairy fanner who is now devoting his time to working on the implement. "I came up with the idea after looking for a way to get more output from my forage harvester. I wanted to build a machine that could put up to 40 ft. of swathed hay into a single windrow. My original design included augers for carrying hay across the blades. But I found that when the blades were set at 45 degree angles, hay slid across them without need for an auger. That's when I realized that gentle handling might be my invention's biggest benefit."
According to Pugliese, the problem with conventional hay rakes is that they tear off nutrient-rich leaves and allow some of the leaves to escape between the tines. "The spinning rollers on my hay windrower are less aggressive than the tines on a rake. The rollers just brush the stubble without letting any hay escape under the blades. The hay moves across the closed body of the blades so there's almost no loss of leaves. Studies show that conventional rakes lose 7% of the leaves on average and even more when the hay is dry. I'm certain that my windrower cuts leaf losses in half.
"Another advantage is that I can operate my windrower at faster speeds without knocking off leaves. The faster you go with conventional rakes, the more leaves you knockoff. Most rake manufacturers recommend a top speed of 5 mph, but I can go up to 7 mph without any problems. In fact, the faster the speed the smoother the hay flows across the blades. Discharged hay falls upside down allowing the windrower to also be used as an inverter."
Pugliese says his biggest concern at rust was hay wrapping around the rollers. However, he hasn't had any problems. He made the rollers by welding 1/4-in. sq. steel bars spaced 1 in. apart all the way around a 3 1/2-in. dia. steel pipe. He bolted an adjust-able 1/4 in. thick, 2-in. high steel plate along the bottom edge of the blades that allows him to adjust the distance between roller and blade. He normally sets the rollers about 1/16 in. from the plate.
"My biggest concern now is how to keep the rollers at the proper height," says Pugliese. "The rollers should just buff the hay stubble. If they're too close to the ground they scalp the stubble in rough areas, and if they're too high they miss some hay. Steel skid shoes are mounted under each blade just behind the roller on the leading edge of the blade. I wish they were adjustable so that I could lower the rollers in close-cut hay. Scalping hasn't been a problem on level fields. However, it is a problem on rough or hilly fields."
Each roller is chain-driven by a hydraulic motor mounted behind the blade. The motors are powered by a 50 gpm hydraulic pump (salvaged from a truck hoist). "The hydraulic pump has more power than I need so I have to run the tractor at half throttle to hold the rollers down to 1,600 rpm's. If the rollers run faster they throw the hay too far," notes Pugliese.
He used the steel frame from an old U-Haul trailer t
To read the rest of this story, download this issue below or click
here to register with your account number.