You have reached your limit of 3 free stories. A story preview is shown instead.
To view more stories
(If your subscription is current,
click here to Login or Register.)
Low-Cost In-Place Shaft Repair
Larry Harrington, L&K Machines, saves his clients big bucks when they have a bad front pulley or a worn crankshaft. Instead of ripping apart the engine and replacing the shaft or trying to machine it, he turns it in place.
“Some old Deere irrigation engines run good, but they’re notorious for the front pulleys f
..........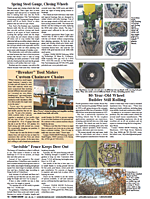
You must sign in, subscribe or renew to see the page.
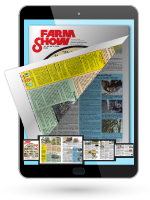
You must sign in, subscribe or renew to see the flip-book
Low-Cost In-Place Shaft Repair ENGINES Larry Harrington L&K Machines saves his clients big bucks when they have a bad front pulley or a worn crankshaft Instead of ripping apart the engine and replacing the shaft or trying to machine it he turns it in place “Some old Deere irrigation engines run good but they’re notorious for the front pulleys falling off when you hang a center pivot generator on it ” says Harrington “Often the crankshaft is worn and wears out the center hole on the old pulley ” He notes that sometimes farmers will buy a new pulley thinking that’ll fix the problem Usually it won’t stay on Even if it does initially it may run for months and then fall off Just taking the crankshaft out and putting it back in can cost more than $1 000 Harrington can fix it and fix the old pulley most of the time for less than the cost of a new pulley Harrington has fixed machinery for over 50 years and has picked up a few tricks along the way In this case he starts with a special jig a steel table that clamps in place close to and parallel to the shaft A slot on the table holds a carbide lathe bit A handle on a rack and gear under the table slides the surface with the bit back and forth The jig makes the bit go in a straight path explains Harrington “I remove the radiator and have to be able to run the engine for about 3 min total ” he says “I run it only a minute at a time for each pass of the bit ” With the engine running Harrington takes his first shallow cut to see if the diameter is the same front and back on the shaft If it is he knows the jig is parallel to the shaft “If it’s not parallel I’ll put a taper on the shaft and I don’t want to do that ” he says “It generally takes three passes to straighten the worn shaft ” Once he’s turned the shaft back into shape he shuts down the engine and measures the shaft with a micrometer to be sure it’s straight Then he goes to work on the pulley “The pulley has to fit the turned shaft ” says Harrington “The hole on the old one is usually worn out and a new one can cost $1 000 ” If the rubber dampener on the old one is still good he bores out the pulley Then he makes a sleeve to fit the gap between the pulley and the shaft He notes that he can often salvage the pulley but even a new one will have to be bored out as it won’t fit the turned shaft “The shaft may have a 30 000th of an inch turned off and I’ll bore that much out of the pulley ” says Harrington “I’ll make a 60 000th of an inch sleeve key it and slip it on the shaft ” Harrington says he’s made the repair on crankshafts more than 10 times in the shop as well as in the field He prefers doing it in the shop where he has all the equipment needed “I’ve never had a failure ” he says “If I can salvage the old pulley I can do the whole job for less than the cost of a new pulley ” Contact: FARM SHOW Followup L&K Machines P O Box 484 Western Neb 68464 ph 402-433-4751; lh44255@windstream net
To read the rest of this story, download this issue below or click
here to register with your account number.