You have reached your limit of 3 free stories. A story preview is shown instead.
To view more stories
(If your subscription is current,
click here to Login or Register.)
Chopper/Roller Mill Combo Blows Ground Corn Into Silo
"It allows me to crack high moisture shelled corn and blow it into my silo without spending the money for an expensive new roller mill that wouldn't do the job any better," says James Skelton, Edinboro, Penn., who mounted a used 1975 Peerless International roller mill on the frame of a 1974 New Holland 770 pull-type si
..........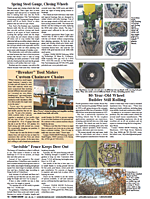
You must sign in, subscribe or renew to see the page.
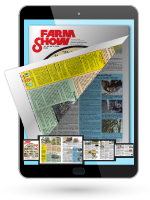
You must sign in, subscribe or renew to see the flip-book
Chopper/Roller Mill Combo Blows Ground Corn into Silo CROP STORAGE Grain Storage 14-1-2 "It allows me to crack high moisture shelled corn and blow it into my silo without spending the money for an expensive new roller mill that wouldn't do the job any better," says James Skelton, Edinboro, Penn., who mounted a used 1975 Peerless International roller mill on the frame of a 1974 New Holland 770 pull-type silage chopper.
Skelton removed the chopper's spout,
cutterhead and knives. He removed the roller mill's electric motor, belts, and pulleys, and mounted the hopper and auger discharge pipes on the chopper frame. A driveshaft off the chopper's pto-driven gearbox powers the roller mill. Corn is augered from gravity wagons into the roller mill hopper which cracks the corn and delivers it into the chopper blower. The blower, hooked up to the silo pipe, blows cracked corn up into Skelton's 20 by 70-ft. silo.
"I had been picking ear corn and using the chopper at the silo to grind and blow it into the silo," says Skelton. "However, I was running short on space for high moisture corn. Rather than build another silo I decided to buy a combine and fill my silo with cracked shelled com to conserve space. A chopper alone doesn't do a good job of crackng shelled corn so I bought the used roller mill for $1,000. It was driven by an electric motor and designed to crack corn after it's unloaded from the silo. By mounting the roller mill on the chopper frame I can crack shelled corn and blow it into the silo for about 1/10 the cost of a new conventional roller mill. Cracking shelled corn before it goes into the silo increased my silo capacity by 50% compared to grinding and blowing ear corn into the silo, and 25% compared to using a silo blower to fill the silo with shelled corn and then cracking it later. My roller mill/silage chopper combo also eliminates the hassle of running an electric motor-driven roller mill every time I unload corn. I can crack a 5-ton load of corn in 15 minutes."
Corn is cracked by two 1-ft. wide rollers inside the roller mill hopper. From there it's augered up through a vertical pipe, then over into a plastic pipe and down into the chopper blower. Skelton welded a metal box to the rear side of the blower and cut a hole in the top for the pipe. The same shearpin that was used on the chopper cutterhead protects the roller mill from damage.
For more information, contact: FARM SHOW Followup, James Skelton, R.D. 1, Box 13380, Edinboro, Penn. 16412 (ph 814 734-1750).
To read the rest of this story, download this issue below or click
here to register with your account number.