2022 - Volume #46, Issue #3, Page #35
[ Sample Stories From This Issue | List of All Stories In This Issue | Print this story
| Read this issue]
Double Bench Grinder Saves Space
![]() |
![]() |
He knew he needed a silicon carbide wheel, wire brush wheel, and a general-purpose wheel to shape a high-speed steel cutter and drill bits.
Bunniss’ solution was a rotating mount for the two grinders.
He explains, “I have the silicon carbide and a regular wheel on one of the grinders, and they take care of any grinding I need to do on a carbide cutter or a high-speed steel, lathe cutters.”
The other grinder is set up with the wire brush and a regular wheel for general grinding.
“To rotate the grinders, I loosen the set screw with the welded ‘tee’ handle, back it out of the hole in the shaft, and rotate it 180 degrees,” says Bunniss. “The mount has a built-in stop which will only allow the platform to turn 180 degrees to the stop and back, which prevents the cords from wrapping up on the post.”
Bunniss built the entire system out of scrap metal. That includes two pieces of pipe, with one machined to fit within the other. As he explains, “I used a 6-in. long by 3-in. OD pipe for the inside pipe that is welded to a 10-in. by 3/16-in. by 18-in. long channel iron for the platform. The outside pipe was machined to a loose fit for the 3-in. OD pipe and then welded to an 8-in. by 10-in. by 1/4-in. wall plate.”
Since the walls of his shop are poured concrete, getting a secure mount was a relatively easy process.
He made the stop by drilling two holes a little over 180 degrees from each other around the circumference of the side pump and then cutting out the metal between them with a metal saw.
Says Bunniss, “I could have accomplished the same thing with the milling machine and the rotary table, but I didn’t think it needed to be that accurate.”
Contact: FARM SHOW Followup, Tony Bunniss, Webster, Minn. (glennlee1964@gofast.am).
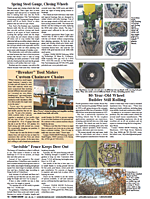
Click here to download page story appeared in.
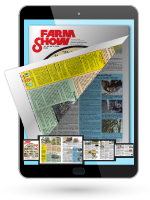
Click here to read entire issue
To read the rest of this story, download this issue below or click here to register with your account number.