You have reached your limit of 3 free stories. A story preview is shown instead.
To view more stories
(If your subscription is current,
click here to Login or Register.)
Wood Wagon Built With “Old” Wheels
A set of old wagon wheels found new life when Dennis Wiard used them to build a wooden wagon. Semi-retired, he still raises some wheat, hay, oats, and other small grains.
“I clean my own wheat for reseeding and thought an old-fashioned wagon would be just right for supplying the seeder,” says Wiard. “I p
..........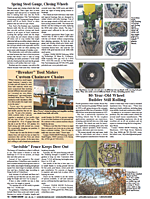
You must sign in, subscribe or renew to see the page.
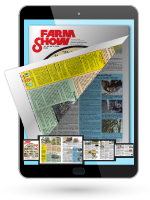
You must sign in, subscribe or renew to see the flip-book
Wood Wagon Built With “Old” Wheels WAGONS/TRAILERS Conversions A set of old wagon wheels found new life when Dennis Wiard used them to build a wooden wagon Semi-retired he still raises some wheat hay oats and other small grains “I clean my own wheat for reseeding and thought an old-fashioned wagon would be just right for supplying the seeder ” says Wiard “I put the wheat in a gravity box before running it through the cleaner From there it goes into the wooden wagon ” The steel wheels still had their wooden spokes and hubs but that was all Wiard visited an Amish neighbor who had some antique wooden wagons He patterned his after them “I have a sawmill and had sawn out some cants from elm trees that had been drying for a year or so ” says Wiard “I cut them to length and then turned them down to cone shaped ends to fit inside the cast iron hubs ” To turn the 6 by 6 in cant ends down Wiard fabricated an oversized lathe that turned at about 100 rpm’s He used a chainsaw to whittle down the ends and then sanded them to fit the hubs “They had to be perfectly concentric at both ends ” says Wiard “Getting them to the exact cone shape was almost impossible so I took some Durham’s Rock Hard Water Putty and shoved it into the hub before inserting the axles The putty filled up any voids I had ” On old wagons a threaded bolt ran through the wooden axle and the hubs When tightened down nuts pulled the axles into the hubs For his new old wagon Wiard ran 3/4-in rebar through the hub and axle to the opposing hub “I welded threaded bolts on each end that I could tighten down to squeeze the hubs onto the axle ” says Wiard He made the main beams for the wagon undercarriage from 4 by 8-in native lumber from his sawmill He attached them to the rear axle and to the fifth wheel on the front axle reinforcing them at the front and rear with cross members to prevent twisting He notes that fabricating the fifth wheel was his biggest challenge He used two 1/4-in thick 15-in diameter steel plates attaching one to the front axle and the other to the undercarriage of the wagon “I added a grease zerk to the fifth wheel to keep it lubricated ” says Wiard A 1-in bolt runs through the plates to tie them together It extends down and through the front axle as well as through the front end of the reach a 4 by 4-in cant that is bolted to the rear axle “It prevents pulling the front axle out from underneath the wagon while letting it turn 60 to 70 degrees” says Wiard The box sides are made of home-sawn cherry boards with a floor of fiberglass over plywood “The floor is real slippery ” says Wiard “A sliding door on the end gate directs small grain seed into a tin funnel I set a 5-gal pail under the funnel to transfer seed to the drill ” A vertical post attached to the front cross member lifts the box to speed unloading The 6 by 6-in steel post was salvaged from a New Holland Haybine A 1-ton hoist that runs through pulleys on the post raises and lowers the box “I dressed up the corners of the wagon box with angle irons from the #7 picker ” says Wiard Contact: FARM SHOW Followup Dennis Wiard 3935 E 450S LaGrange Ind 46761 ph 260 350-7932
To read the rest of this story, download this issue below or click
here to register with your account number.