You have reached your limit of 3 free stories. A story preview is shown instead.
To view more stories
(If your subscription is current,
click here to Login or Register.)
Grind Ear Corn Right In The Field
Ohio dairy farmer Bob Koerner, of Edgerton, liked the idea of mixing high moisture ground ear corn with regular corn silage for his 250 milking Holsteins. But he wasn't satisfied with the slow harvest pace of a 2 row picker and grinding corn at the silo.
To speed things up, he bought a 6 row Vermeer corn picker (
..........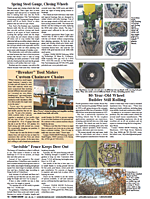
You must sign in, subscribe or renew to see the page.
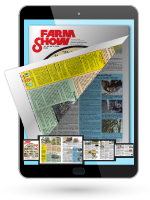
You must sign in, subscribe or renew to see the flip-book
Grind Ear Corn Right In The Field LIVESTOCK Feeding Equipment 6-4-29 Ohio dairy farmer Bob Koerner, of Edgerton, liked the idea of mixing high moisture ground ear corn with regular corn silage for his 250 milking Holsteins. But he wasn't satisfied with the slow harvest pace of a 2 row picker and grinding corn at the silo.
To speed things up, he bought a 6 row Vermeer corn picker (30 in. rows) shortly before harvest last fall and now grinds ear corn in the field as it's picked.
The Vermeer picker, manufactured by Vermeer Mfg., Pella, Iowa, is designed for rear-mounting on 2-wheel drive tractors. Koerner wanted it on a 4-wheel drive Case 2690. Also, because of the limited range of reverse speeds in the 2690, he wanted the tractor to travel forward in the field instead of in reverse. This problem was solved by mounting the picker on a bulldozer frame on the front of the tractor. Koerner also discovered that the tractor was longer than most tractors on which the picker is mounted and special 40 in. elevator extensions had to be ordered from Vermeer to carry corn from the picker to the rear of the tractor. (One elevator on each side of the tractor carries corn from three rows of the picker.)
But, Koerner still wanted ground ear corn, and Vermeer offers only a husking bed or a sheller attachment for the picker. So, he bought a used Gehl 800 recutter and modified the discharge blower location to permit easier delivery of ground corn to forage wagons trailed behind the tractor. The grinder is driven by a pto shaft running directly to the cutterhead.
The picker was first used to open fields before Koerner started chopping silage with a pull-type forage harvester. Even though moisture content of the corn was probably close to 40%, Koerner says performance was satisfactory and that the corn was simply mixed with the silage. To grind corn that wet, the screens were completely removed from the grinder.
Koerner says he prefers moisture content of the ground ear corn to be 27 to 32%, all kernels cracked and the cobs well shattered. When he first started field-grinding corn for storage, a 2 in. screen was used in the grinder. Later, when moisture dropped to about 26%, a 1 in. screen was installed.
"The grain mixes better with silage if all kernels are cracked and cobs are broken into small pieces," says Koerner. "This also helps prevent cows from sorting grain from the silage as they eat. Most pieces of cob were the size of a pea or smaller."
"We normally travel 2-3 mph with the 6-row harvester," says Koerner, "compared to 3 1/2 to 4 mph with the old 2-row picker. But, with the wider machine and much less labor required at the silo, we can now harvest and store more than twice as much corn per day, and nobody has to work as hard as they did before. One man feeding the grinder at the silo really had to keep jumping to keep up with the 2-row picker, and we usually had to have someone else running wagons back and forth. Now, one man hauls and unloads into the blower, so there's really a big difference in work required. We can field-grind about 20 acres per day in corn yielding 130-140 bu. per acre."
The 6-row Vermeer picker cost Koerner about $20,000 including the modified elevators (compared to roughly $10,000 for a new 2-row picker), and the used grinder cost another $3,000.
For more information, contact: FARM SHOW Followup, Bob Koerner, Edgerton, Ohio 43517 (ph 419 298-2049).
To read the rest of this story, download this issue below or click
here to register with your account number.