1978 - Volume #2, Issue #2, Page #27
[ Sample Stories From This Issue | List of All Stories In This Issue | Print this story
| Read this issue]
Bale Compactors Catching On Fast
![]() |
Other Wisconsin hay dealers who've seen the Spiegelberg Squeezer demonstrated are generally agreed that bale compactors of one form or another will soon be used to process virtually all baled hay being transported long distances.
The Spiegelberg squeezer is one of the first portable units to hit the market. "Here in the midwest you need portability so the compactor can be moved to wherever the hay is located," says Spiegelberg. He notes that a pilot model of his compactor has been field tested. A refined and fully automated production model is slated for unvieling this summer, he told FARM SHOW. It takes two persons to operate his prototype compactor. Capacity is right at 4 bales in and 2 out every minute, or about 120 compacted bales per hour. Two conventional sized bales, weighing 50 to 60 lbs. each, are pressed into a single compacted bale which has the same dimensions as a standard bale except that it weighs twice as much (100 to 120 lbs.), allowing trucks to carry heavier payloads and thus reduce transportation costs. Twine is left on the original bale. Individual compacted bales are tied with wire to hold them intact for transport.
"The machine makes a perfect bale every time. They are nice to load and customers don't seem to mind having to lift the extra weight of compacted bales. The compactor has a gentle action which causes very little leaf shattering, thus maintaining quality," explains Spiegelberg. He notes that the new bale compactor slated for introduction later this year will have a capacity of 8 conventional bales in, and 4 compacted bales out per minute. An apron will automatically feed bales into the unit, and compacted bales will be automatically tied with wire.
One of the pioneer builders of bale compactors is Ken Jensen, of Ellensberg, Wa. He serves as a consultant on custom-built bale compactors, and designed and built the huge stationary compactor which he operates on a custom bases for the Anderson Hay and Grain Company, at Ellensberg. He notes that conventionall bales weighing 100 to 120 lbs. are compacted to half their original size. The Jensen-built compactor processes right at 47 tons of baled hay per hour and costs $60,000 to $75,000. One
man feeds bales into the compactor, one removes wire or twine from the original bales, and a third person handles and stacks the compacted bales. The compactor is operated by a 200 hp. electric motor and automatically wraps each compacted bale with a wire strap.
Jensen notes that interest in bale compacting on the West Coast has been up and down, depending on export demand for hay, particularly to Japan. Bales destined for export are loaded onto 40 ft. long containers which are trucked to ports and loaded directly onto ships. Jensen adds that compacting also has allowed hay growers to ship baled hay more economically in railroad box cars. Current regulations require at least 30 tons of weight per boxcar, which is impossible without pressing conventional bales into smaller packages so more hay can be loaded into each car.
Attempts to make compacted bales right in the field, thus eliminating the need for a second rebaling operation, have generally been unsuccessful. "It doesn't work to make tight, compacted bales right in the field," explains Jensen. "Hay has to go through a 3 to 4 week curing before it can be squeezed together into a compact bale."
If you'd liken compare notes with Jensen on custom built bale compactors, contact: FARM SHOW Followup, Ken Jensen, do Anderson Hay and Grain Company, Box 99, Ellensberg, Wa. 98926 (ph. 509 925-9818).
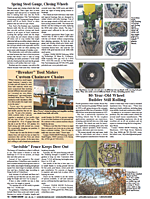
Click here to download page story appeared in.
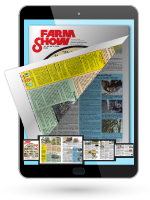
Click here to read entire issue
To read the rest of this story, download this issue below or click here to register with your account number.