You have reached your limit of 3 free stories. A story preview is shown instead.
To view more stories
(If your subscription is current,
click here to Login or Register.)
Dozer Tracks Used To Make Shop Apron
Farmers keep finding new uses for old stuff at Damon Carson’s company, Repurposed Materials, which recycles industrial materials on a giant scale (www.repurposedmaterials.com). Carson recently sent photos of a project done by one of his customers, Jaime Stuever of Bailey, Colo. He used lengths of bulldozer rubber track
..........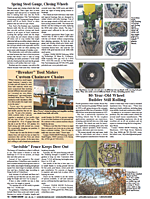
You must sign in, subscribe or renew to see the page.
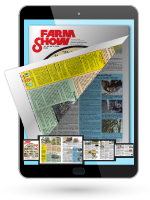
You must sign in, subscribe or renew to see the flip-book
Dozer Tracks Used To Make Shop Apron TILLAGE EUIPMENT Accessories Farmers keep finding new uses for old stuff at Damon Carson’s company Repurposed Materials which recycles industrial materials on a giant scale www repurposedmaterials com Carson recently sent photos of a project done by one of his customers Jaime Stuever of Bailey Colo He used lengths of bulldozer rubber track tread to build a 16-ft wide 27-ft deep apron in front of his new workshop “My tire tread apron took only about 4 hrs to install and saved thousands of dollars in concrete work It cost only about $900 ” says Stuever “The tread is heavy and solid so it won’t go anywhere in high winds even though it’s not anchored down I’m very happy with it ” He says the tread was made by Firestone and looked new with the factory tags still on it “There must have been blemishes on it or some other kind of problem but I didn’t notice anything wrong It came with a diamond-shaped pattern and was just what I wanted so I took all the tread the company had I could have used even more if it had been available ” The tread came in 16-ft long 3-ft wide sections that were 3 in thick Each section weighed about 300 lbs Stuever drove to the company’s Denver headquarters last November and loaded 9 tread sections onto his single axle flatbed trailer At home he used a fork-equipped loader bucket to unload the sections one at a time centering each section on the forks with both ends drooping down “It was cold the day I installed the apron so the sections were a little stiff but it wasn’t a problem ” says Stuever “I got off the tractor and pushed both ends of the section down by hand a little at a time By maneuvering the loader I was able to fit the sections tightly together ” He says the tread is pliable enough that it conformed nicely to the ground contour Before installing the apron he used a hoe and shovel to level the area making sure the tread would be level with the entryway to the shop He says wind and snow hasn’t caused any problems “We had wind gusts this winter of more than 80 mph but the tread didn’t move at all We also had about 100 in of snow Whenever it snowed I used a loader bucket to remove most of the snow from the apron The shop faces south and with its black color the tread heats up in the sun and quickly melts the snow The water drains into the ground between the tread sections so there are never any icy spots ” Stuever also bought some old conveyor belts from Repurposed Materials and used them to make an inexpensive “sidewalk” leading to his house as well as a patio behind it He simply laid two 15 by 3-ft sections down end to end “The belts look nice and have a link-style design that makes them easy to clean with a broom ” he says “They’re made of hardened plastic and can take a lot of abuse ” He used 2 more belts to make the patio “I placed the belts on a sawhorse and used a hacksaw to cut them in half then laid them side by side on the ground to make a 7 1/2-ft rectangle The belts have a greenish color so they look nice I paid $20 apiece for them ” Stuever says he plans to also install conveyor belts on the concrete floor next to his shop workbench “I think they’ll work great because they’ll be softer to stand on and will insulate the floor to keep it from feeling so cold during winter ” Contact: FARM SHOW Followup Jaime Stuever 1373 Delwood Dr Bailey Colo 80421 ph 719 838-0789; hoochmeister@yahoo com
To read the rest of this story, download this issue below or click
here to register with your account number.