2018 - Volume #42, Issue #3, Page #29
[ Sample Stories From This Issue | List of All Stories In This Issue | Print this story
| Read this issue]
He Built A Self-Propelled Stump Grinder
![]() |
![]() |
His stump grinder has no expensive hydraulics and instead relies on the mower’s gas engine and a pair of identical electric starter motors off old riding mowers. One motor is used to start the engine and the other to power the mower’s transaxle, which drives the machine. Both starter motors operate off the mower’s battery.
He started with an old Cub Cadet mower equipped with an 18 hp. electric-start horizontal shaft gas engine and 5-speed transmission. He stripped the machine down to just the engine, battery, transaxle and wheels. He used steel tubing to build a rectangular frame and mounted the engine and transaxle on back of it.
He cut off all but the center portion of a small pulley at the middle of the transaxle and welded the drive gear off a Briggs & Stratton starter motor onto it. He fastened the starter motor itself upside down next to the drive gear, and it drives the transaxle. “The starter motor stays engaged to the transaxle at all times,” says Ranta. “If I want I can drive the machine around without even running the engine.”
He remounted the engine’s original starter motor horizontally a few inches behind the other starter motor and hooked it up to a solenoid valve that replaces the engine flywheel.
He welded a pair of handlebars off a rototiller on back of the frame, keeping the rototiller’s throttle choke and ignition switch. A push button is used to engage the motor that drives the transaxle. A T-shaped chrome lever serves as a parking brake by locking the transaxle up.
He bought 12 Rayco stump grinder teeth from Bailey’s (www.baileysonline.com) and bolted them onto a 48-tooth, No. 60 chain sprocket. The sprocket mounts on pillow block bearings that ride on a 1 1/2-in. dia. driveshaft attached to the front part of the frame.
“I mounted a small pulley on the engine and a larger one on the driveshaft to make the sprocket run slower,” says Ranta. “A spring-loaded idler pulley is used to engage a pair of belts that drive the sprocket. The idler pulley is controlled by a long metal rod with a golf ball fixed to one end that leads back to the handlebars.”
The sprocket is covered by a metal shield that deflects wood chips to the side instead of back toward the engine and battery.
“It works even better than I thought it would,” says Ranta. “I got the engine free from a friend and spent less than $500 to build it. I built it because I wanted to help a friend remove several big stumps in her back yard. A local contractor wanted $400 to grind them down.
“I had to install the starter that drives the transaxle upside down because it wouldn’t fit any other way. A starter motor won’t run long before it heats up so I can’t drive the machine around for very long, but that isn’t a problem.”
Contact: FARM SHOW Followup, Kenny Ranta, 1711 Wornall Rd., Excelsior Springs, Mo. 64024 (ph 816 536-6320; kiranta1@yahoo.com).
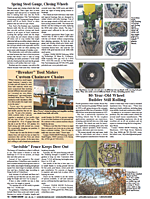
Click here to download page story appeared in.
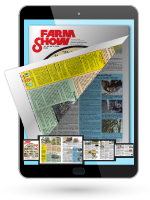
Click here to read entire issue
To read the rest of this story, download this issue below or click here to register with your account number.