You have reached your limit of 3 free stories. A story preview is shown instead.
To view more stories
(If your subscription is current,
click here to Login or Register.)
Self Steer System For Deere Chopper
"It automatically keeps our forage harvester on the row and cost less than $20 to build," say Ivan and Roy Zimmerman, Denver, Penn., about the home-built row guidance system they added to their Deere 3940 2-row, 38-in. row pull-type forage harvester.
The Zimmermans patterned their system after a commercial guida
..........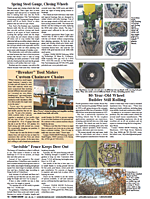
You must sign in, subscribe or renew to see the page.
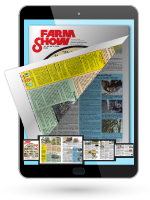
You must sign in, subscribe or renew to see the flip-book
Self steer system for Deere Chopper HAY & FORAGE HARVESTING Forage Harvesters 14-3-4 "It automatically keeps our forage harvester on the row and cost less than $20 to build," say Ivan and Roy Zimmerman, Denver, Penn., about the home-built row guidance system they added to their Deere 3940 2-row, 38-in. row pull-type forage harvester.
The Zimmermans patterned their system after a commercial guidance system that wasn't available for their chopper model. Spring-loaded sensors mounted on the snout of the harvester deflect when hit by stalks of corn. This sends a signal to the hydraulic tongue positioner, which moves the harvester back on the center of the row.
"Our system keeps the harvester from slipping off the row and eliminates the stress of always having to look back, even on curving rows," says Roy. "The tongue automatically moves as much as 24 in. from side to side. Even when making a sharp turn at the end of the field, the harvester always stays on the row.
"We bought the forage harvester used. It already was equipped with a bank of 4 hydro-electric valves and a hydraulic tongue swing cylinder. The 4 valves, operated by switches mounted on a control box on the tractor, are designed to control the forage harvester's deflector, header height, spout, and feed rolls. The tongue swing is designed to be operated by a second hydraulic valve and dual outlet on the tractor. However, we didn't have a second valve nor did we want to spend the money on one. So we disconnected the valve that controls the chopper feed rolls and used the extra valve to power the tongue swing cylinder. We seldom use the feed rolls while chopping so it's no bother to operate them manually for sharpening. The tongue swing valve is controlled by a pair of microswitch sensors mounted on the chopper snout."
Zimmerman notes that he actually disconnected both the feed rolls and deflector valve controls. He uses the feed roll valve to run the deflector and the deflector valve to run the tongue swing because the feed roll valve didn't have enough pressure to operate the tongue swing.
The row sensors consist of a pair of 1 1/ 2-in. wide, 1/8-in. thick, 3-ft. long flat spring steel springs removed from the head of an old Allis-Chalmers forage harvester. One end of each spring bolts to the front end of the harvester's snout. A microswitch mounts on each side of the snout and is wired to the valve controlling the tongue. When the spring deflects against stalks of corn, it causes the microswitches to send signals to the hydraulic tongue positioner which automatically moves the harvester back on the center of the row.
A 3-in. long rubber piece on the ends of both steel springs eliminates any clattering noise. Zimmerman notes that the curvature of the springs is critical so that they won't bounce in andoutbetween stalks. His springs have an 8-in. long "flat spot" that runs against the stalks. In narrower rows the flat spot might have to be 12 in. long if plants were spaced further apart within the row.
Contact: FARM SHOW Followup, Ivan Zimmerman, RD 1, Box 408, Denver, Penn. 17517 (ph 215 267-2459).
To read the rest of this story, download this issue below or click
here to register with your account number.