2016 - Volume #40, Issue #2, Page #33
[ Sample Stories From This Issue | List of All Stories In This Issue | Print this story
| Read this issue]
Conduit Reels Make Great Bale, Grain Feeders
![]() |
![]() |
![]() |
“They’re hard to find, but I knew a guy who had access to some,” says Jost.
Each 8-ft. dia. reel side is formed from steel rings and eight, 4-ft. steel spokes that join at the center. Jost cut the spokes away and used his 6-in. grinder to smooth rough spots on the rings.
Using the rings and spokes, he made a fairly standard size bale feeder for the friend who provided the reels. He also built a shorter one for his own Lowline Angus. Between their smaller size and horns on some, a standard full-size feeder doesn’t work.
“Both feeders have a lower section made from two rings and 16-in. lengths of spokes,” says Jost. “I bought 16-in. wide strips of 18-gauge steel and welded it to the outside of the rings. I wanted it heavy enough to weld, to stand up to the cattle and to move around with a bale spear on my loader.”
To finish his friend’s full-size bale feeder, he added a third ring. Spreader bars mounted at an angle between the second and third ring give it a full height of about 45 in.
For the upper portion of his own feeder, Jost recycled U-shaped hoops from some old Durabilt bale feeders. They were the right height and allowed an animal with horns to feed without getting snagged as he pulled away.
“I saw the Durabilt feeders in a pile at this farm,” explains Jost. “I stopped and offered the owner $10 for the lot, and he took it and then gave me some more hoops stacked up against a silo.”
The hoops were still solid, though the remainder of the Durabilts was rusted out. “I broke the hoops off and welded them to the top of the feeder rings,” says Jost. “I ended up with enough hoops to make 2 more bale feeders.”
Jost says the rings from the conduit reels have worked great for other projects as well. He fabricated a rounded steel roof over a feed wagon/feeder. He cut 5 rings to match the width of the wagon, added cross members and covered it with steel roofing. The half circle front end was cut from steel, while the rear end was made from wood with a door for checking feed levels. Jost made a top fill door, mounting it to rings at the front of the wagon.
Other changes to the wagon turned it into a feeder that handles the 8 head Jost normally feeds out each year. He replaced the rusted out floor with tongue and groove flooring and added a feeder tray at the back end using an auger tray from a scrapped out chopper. Jost designed a manual unloading auger, allowing him to move the feeder wagon as needed.
“I bought a 4-in. auger at auction for $50, removed the motor and cut holes in the top of the auger tube,” he said. “I cut a hole in the back end of the wagon and shoved the auger through.”
With the auger reaching from one end to the other it can gather feed the length of the wagon. To fill the feeder tray, Jost simply turns the drive pulley by hand. To make it easier, he added a steering wheel knob.
“I just crank it round like a steering wheel to fill the feeder tray,” says Jost. “It’s a flat floor so at some point I have to go inside and shovel feed to the end.”
He says one fill of the feeding tray is about what his calves will eat in a day. While he could have automated it, the manual nature has an added benefit.
“I like to get into the yard with them to see how they are doing each day,” says Jost. “Having to fill the tray makes sure I do.”
Contact: FARM SHOW Followup, Dan Jost, 17992 Co. Rd. 49, Richmond, Minn. 56368 (ph 320 980-6176).
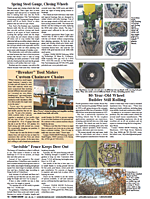
Click here to download page story appeared in.
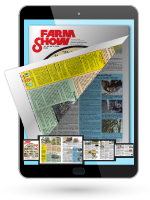
Click here to read entire issue
To read the rest of this story, download this issue below or click here to register with your account number.