You have reached your limit of 3 free stories. A story preview is shown instead.
To view more stories
(If your subscription is current,
click here to Login or Register.)
Building A Big One-Piece Door Saved Lots Of Dollars
Kin Purvis is a South Carolina do-it-yourselfer who isn’t afraid to tackle big projects. When he needed a door for the 50-ft. wide opening on his airplane hangar, he and his friend, Ted Parker, built it themselves. Says Purvis, “I saw hangars with split doors folding up and out or up and in, but that style wouldn’t
..........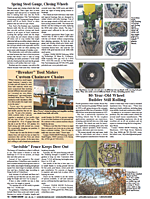
You must sign in, subscribe or renew to see the page.
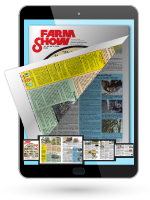
You must sign in, subscribe or renew to see the flip-book
Building A Big One-Piece Door Saved Lots Of Dollars BUILDINGS Accessories Kin Purvis is a South Carolina do-it-yourselfer who isn’t afraid to tackle big projects When he needed a door for the 50-ft wide opening on his airplane hangar he and his friend Ted Parker built it themselves Says Purvis “I saw hangars with split doors folding up and out or up and in but that style wouldn’t work for my building Besides they cost several thousand dollars I needed a one-piece door that would provide more clearance for the plane to get in ” After getting some ideas from a home-made door they saw in Virginia Purvis and his friend drew up their own plans They built the framework for the 12-ft high by 50-ft wide door on the floor of the hangar using 2-in square tubing The “grid” they developed consisted of 10 by 4-ft sections Diagonal reinforcing pieces of 1/2-in rod were welded into several sections When the frame was done they covered the outside with the same metal siding used on the sides and back of the hangar Purvis and Parker also built the track and opener for the door “We stood the door up and mounted rails like those on a barn door across the top The hinged ends were loose so the door could easily lift from the vertical to a horizontal position Raising and lowering the door is done with a winch that is normally used to raise and lower feeders in a large poultry barn The winch is mounted to the ceiling of the building on a reinforced plank Purvis uses a 1/2-in Milwaukee power drill connected to an 8-ft long handle to operate it He used another brand drill at first but found the Milwaukee had more torque The door is lifted by 1/4-in cables connected to loops on the frame about 4 ft from the bottom The cables roll on and off the spool under the winch as the 600-lb door is opened and closed Purvis says the cable powers in and out without overlapping or tangling because they installed a center divider on the spool After completing the project Purvis and his friend learned that the single winch system wouldn’t raise the door when it was fully closed To solve that problem they made a hand turning winch that lifts the door from straight vertical to about 10 to 15 degrees horizontal When the door is closed the small winch also locks it in place Says Purvis “We break it open using the small winch with the hand crank then turn it over to the power winch and that raises the door fully open in about a minute ” The big door project took about a week to complete and Purvis says it probably cost about $700 less than a third what a bi-fold with a power opener would cost A large part of Purvis’s cost was buying the winch and the high torque Milwaukee Magnum drill which has more than enough power to operate the winch Purvis also installed 20-lb counter weights on each end of the door lift so there’s less power needed to raise it Contact: FARM SHOW Followup Kin Purvis 203 Hamlin Rd Aiken S Car 29805 ph 803 648-7295; kinpurvis@bellsouth net
To read the rest of this story, download this issue below or click
here to register with your account number.