You have reached your limit of 3 free stories. A story preview is shown instead.
To view more stories
(If your subscription is current,
click here to Login or Register.)
Rollaway Dump Bed Installs When Needed
Jerry Maddock turned his Chevy S-10 pickup into a mini-dump truck with a rollaway dump bed. When not needed, he just rolls it off the S-10 and onto a wheeled cart for storage.
“Sometimes I need a little sand or gravel to mix up a small batch of concrete,” says Maddock. “I have a heart condition and don’t wan
..........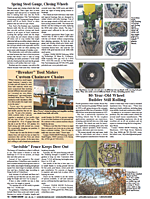
You must sign in, subscribe or renew to see the page.
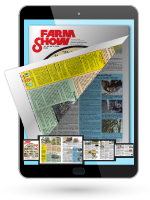
You must sign in, subscribe or renew to see the flip-book
Rollaway Dump Bed Installs When Needed PICKUPS Accessories Jerry Maddock turned his Chevy S-10 pickup into a mini-dump truck with a rollaway dump bed When not needed he just rolls it off the S-10 and onto a wheeled cart for storage “Sometimes I need a little sand or gravel to mix up a small batch of concrete ” says Maddock “I have a heart condition and don’t want to shovel too much ” Maddock had junked out an old GM truck with a hoist but kept the hoist and hydraulic pump He thought about putting it on a trailer but didn’t want to deal with backing it up “The S-10 didn’t have room under the bed to mount it ” says Maddock “So I built a unit that just slides into the S-10 box ” That meant keeping the profile as low as possible Maddock used BobCAD CNC software to place the pump and hoist in the S-10 box digitally and then designed the frame around it Using home sawn lumber he made a double wall subframe to spread the weight across the entire pickup box An upper frame supports the floor and sides of the dump box which extends beyond the bumper “I didn’t want to have to clean the bumper off every time I dumped ” says Maddock “The width and length of the dump bed was designed to match the S-10 box even to the ribs in the floor It just barely fits inside the wheel wells ” The lower frame that houses the hoist and pump was made from 1 5/8-in by 4 1/4-in boards The upper frame is 1 5/8-in by 3 1/2-in boards The sideboards of the dump box are 3/4 in by 7 1/4 in “I used cutouts in the subframe and used a planer to size the wood exactly to provide minimal clearance for the hoist ” says Maddock “I wanted to keep the profile as low as I could ” In key spots where additional support was needed Maddock used flat steel as well as 1/4 in thick 3-in angle iron The angle iron was used to frame the wood at lift points and at the pivot Fabrication included mounts for the hydraulic hoist as well as for the rear pivot point “About the only thing I bought were the bolts and nuts and 4 come-alongs ” says Maddock “Everything else was designed on the BobCAD and cut out with a plasma cutter If there were multiple pieces like on the rear pivot I made a template first ” The come-alongs are mounted at the corners of the pickup box and designed to hold the subframe down and in place Blocks of wood drop into place to either side of the subframe front and back to keep the dump box from moving side to side “Between the come-alongs and the blocks I can hit a bump with the truck and not even know it’s there ” says Maddock “It doesn’t move ” Maddock added 4 retractable wheels to roll the box in and out These too were fabricated in his shop The wheels are on a hinged plate A threaded rod at the end of the plate opposite the pivot pushes the wheels down or pulls them up “When pushed down the wheels ride between ribs on the pickup box bed says Maddock “This ensures the dump box bed rolls straight in and straight out I matched the ribs on the storage cart ” The pump for the hoist is electric Maddock installed a main power line for the pump He ran a smaller wire from the pump’s controls to a toggle switch on the dash Both have quick connects “It only takes a few minutes to remove the dump box bed ” says Maddock “I disconnect the wires and the come-alongs pick up the wood blocks lower the wheels and slide it out ” Contact: FARM SHOW Followup Jerry Maddock 29197 Standley Rd Defiance Ohio 43512 ph 419 395-1594; jmachine@ayersvilletelco com
To read the rest of this story, download this issue below or click
here to register with your account number.