Rebuilding Old Scrapers Is A Family Business
“In the early 1990s I started rebuilding old scrapers for excavating ponds and other projects,” says Arkansas handyman Robert Bass. “Seems like every time I got one rebuilt, someone came along and wanted to buy it, so I decided to make it a full time business.” After 23 years of perfecting his techniques, Bass says now he’s fairly sure his company is the only full time scraper rebuilder in the country. As the elder statesman of the business, he’s on the road more than 140 days a year looking for equipment his company can renovate, repair and resell. His 23-year-old son Travis now heads up the restoration side of the business. Bass’ wife and daughter handle office duties. They also have 4 other employees who’ve worked with them for several years and are experts at rebuilding heavy equipment.
“Eight years ago we went at the rebuilding business full time, and that was also the last time we moved dirt commercially,” says Bass. “We work almost exclusively on Reynolds scrapers ranging from 6 to 20 yd. models. We buy and sell throughout the country and also handle used Deere, IMC, Harvey and Prime equipment.”
Bass says they try to keep an inventory of 40 to 60 scrapers on hand, and typically refurbish 6 to 8 machines a month. Smaller units require about 100 hrs. of work, and larger machines that are more torn up might require 250 to 300 hrs. Some customers want only minor repairs and the company will do that, too.
“We bring equipment in and completely disassemble it, rebuild the cylinders, and install new fittings, pipes and hoses,” Bass says. “We repair dirt pans by using a gouger to cut out old welds, cracked metal and weak metal that’s bent or broken.” Bass says they do that because they learned a long time ago that weld-overs and small patches don’t work in the long run. “Our goal is to rebuild the metal as strong and as good as new. When they leave our shop they look like they just came from the factory.”
Most of their rebuilt equipment is sold to farmers and ranchers who excavate their own ponds, waterways and soil berms. Bass says one of his customers in 2013 had a special request. “The fellow wanted 6 identical 17-yard machines, which was quite an order. He requested new side plates, heavier cylinders and new tires. We averaged more than 300 hrs. on those machines, probably more than it took to build them originally.”
Rebuilt machines typically are good for 2,500 hrs. of work before needing another overhaul. Bass says a typical rebuilt 17-yd. scraper sells for $40,000 to $45,000, compared to $75,000 to $85,000 for a new one.
“Our employees take a lot of pride in their work, and it shows,” says Bass. “Our repair work and paint jobs look better than on new machines.” Most of the equipment they use in the shop to move and handle heavy scrapers is hand-built. They also use plasma torches, cutters, wire welders, stick welders and gas torches. Last year they wore out about 40 hand-held grinders.
Bass says that even though he’s been in the business 23 years, his son Travis is now the driving force, and is enthusiastic about keeping things rolling into the future. “We have a real niche, and our customers are just salt of the earth,” says Bass. “I couldn’t ask for a more rewarding business.”
Contact: FARM SHOW Followup, Robert Bass, 255 Jones Rd., Beebe, Ark. 72012 (ph 501 626-5884; rsbass@ymail.com; www.rsbass.com).
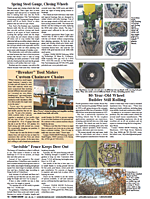
Click here to download page story appeared in.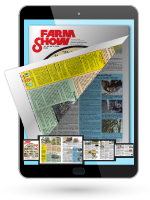
Click here to read entire issue
Rebuilding Old Scrapers Is A Family Business MISCELLANEOUS EQUIPMENT Earth Movers “In the early 1990s I started rebuilding old scrapers for excavating ponds and other projects ” says Arkansas handyman Robert Bass “Seems like every time I got one rebuilt someone came along and wanted to buy it so I decided to make it a full time business ” After 23 years of perfecting his techniques Bass says now he’s fairly sure his company is the only full time scraper rebuilder in the country As the elder statesman of the business he’s on the road more than 140 days a year looking for equipment his company can renovate repair and resell His 23-year-old son Travis now heads up the restoration side of the business Bass’ wife and daughter handle office duties They also have 4 other employees who’ve worked with them for several years and are experts at rebuilding heavy equipment “Eight years ago we went at the rebuilding business full time and that was also the last time we moved dirt commercially ” says Bass “We work almost exclusively on Reynolds scrapers ranging from 6 to 20 yd models We buy and sell throughout the country and also handle used Deere IMC Harvey and Prime equipment ” Bass says they try to keep an inventory of 40 to 60 scrapers on hand and typically refurbish 6 to 8 machines a month Smaller units require about 100 hrs of work and larger machines that are more torn up might require 250 to 300 hrs Some customers want only minor repairs and the company will do that too “We bring equipment in and completely disassemble it rebuild the cylinders and install new fittings pipes and hoses ” Bass says “We repair dirt pans by using a gouger to cut out old welds cracked metal and weak metal that’s bent or broken ” Bass says they do that because they learned a long time ago that weld-overs and small patches don’t work in the long run “Our goal is to rebuild the metal as strong and as good as new When they leave our shop they look like they just came from the factory ” Most of their rebuilt equipment is sold to farmers and ranchers who excavate their own ponds waterways and soil berms Bass says one of his customers in 2013 had a special request “The fellow wanted 6 identical 17-yard machines which was quite an order He requested new side plates heavier cylinders and new tires We averaged more than 300 hrs on those machines probably more than it took to build them originally ” Rebuilt machines typically are good for 2 500 hrs of work before needing another overhaul Bass says a typical rebuilt 17-yd scraper sells for $40 000 to $45 000 compared to $75 000 to $85 000 for a new one “Our employees take a lot of pride in their work and it shows ” says Bass “Our repair work and paint jobs look better than on new machines ” Most of the equipment they use in the shop to move and handle heavy scrapers is hand-built They also use plasma torches cutters wire welders stick welders and gas torches Last year they wore out about 40 hand-held grinders Bass says that even though he’s been in the business 23 years his son Travis is now the driving force and is enthusiastic about keeping things rolling into the future “We have a real niche and our customers are just salt of the earth ” says Bass “I couldn’t ask for a more rewarding business ” Contact: FARM SHOW Followup Robert Bass 255 Jones Rd Beebe Ark 72012 ph 501 626-5884; rsbass@ymail com; www rsbass com
To read the rest of this story, download this issue below or click
here to register with your account number.