Agitation Boat Stirs Up Manure Lagoons
“There are probably 8 to 10 companies building manure agitation boats, but none of the machines I looked at had the features I wanted, so I built my own,” says Wisconsin custom applicator Chris Lindstrom. The project wasn’t too large or complicated for him because his other company, Maxville Truck & Repair, is already involved in repairs and renovation. Since 2002 they’ve built about a dozen custom silage trucks and grain or manure handling vehicles every year, converting trucks and semi tractors.
“The agitation boats I looked at did a decent job, but I thought they needed better pressure control and better handling features,” Lindstrom says. The one he built uses a powerful hydrostatic transmission system mated to 2 Italian-made Veneroni pumps, which Lindstrom thinks are the best on the market. “I can use the hydrostatic drive to change the speed of the pumps to increase agitation, and I can also reverse direction,” he says.
The frame of his agitator is made from 5 and 6-in. schedule 40 pipe along with 3-in. channel iron. The rig is 10 ft. wide, 20 ft. long and weighs about 14,000 lbs. The engine and fuel tank are mounted in the middle. The pumps are mounted fore and aft on swivel joints from old cement trucks. Flotation tanks on each side are filled with styrofoam.
His rig is powered by an L10 Cummins diesel engine that produces 310 hp. Lindstrom and his crew removed it from an old concrtete mixing truck and overhauled it before re-assembling it on the agitator frame.
Lindstrom used his custom-built agitator boat about 400 hrs. during the 2013 pumping season and considered the project very successful. “I can stir up an 8 million gal. pit in 8 hrs.,” he says. “The hydro power lets me turn the agitator in a circle, thrust sidewise, fore and aft and rotate 180 degrees to disintigrate a crust or dislodge materials on the bottom. The pumps output 2,500 gals. per minute at about 45 lbs. psi through 3 and 3 1/2-in. lines.”
The agitator has another very unique feature. Lindstrom says he can remove a nozzle from one of the pumps, attach a hose and feed slurry into a vehicle on the side of the pit. Large tankers are filled in about 3 min.
Lindstrom uses a process control computer to run the machine. It reads pressure on the lines and at the engine, then sends electronic signals through solenoids to actuators that run controls on the hydrostat. Valves are proportional to accept a pulse-less signal from the solenoid. Speed is adjusted by pressing and holding or releasing buttons on the remote actuator. The left-right action of the pump heads is controlled by hydraulic cylinders and the fore-aft movement with a chain and sprocket.
“Running the agitator is like playing a video game,” says Lindstrom. “I’m okay running it, but a 13 or 14 year-old kid who grew up on video games would be fantastic. It’s just a matter of tapping buttons to thrust the boat, control speed and direction.”
Lindstrom isn’t sure how many hours it took to build the machine or what the cost is, but he’s quick to say, “I know it’s a lot less than buying one of those on the market. It was worth every penny because it saves us the use of several tractors and portable pumps.”
Contact: FARM SHOW Followup, Chris Lindstrom, Maxville Truck & Repair, S460 State Road 25, Durand, Wis. 54736 (ph 715 672-7867).
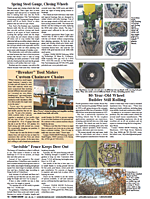
Click here to download page story appeared in.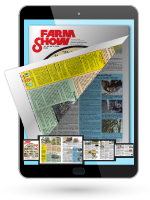
Click here to read entire issue
Agitation Boat Stirs Up Manure Lagoons MANURE HANDLING Equipment “There are probably 8 to 10 companies building manure agitation boats but none of the machines I looked at had the features I wanted so I built my own ” says Wisconsin custom applicator Chris Lindstrom The project wasn’t too large or complicated for him because his other company Maxville Truck & Repair is already involved in repairs and renovation Since 2002 they’ve built about a dozen custom silage trucks and grain or manure handling vehicles every year converting trucks and semi tractors “The agitation boats I looked at did a decent job but I thought they needed better pressure control and better handling features ” Lindstrom says The one he built uses a powerful hydrostatic transmission system mated to 2 Italian-made Veneroni pumps which Lindstrom thinks are the best on the market “I can use the hydrostatic drive to change the speed of the pumps to increase agitation and I can also reverse direction ” he says The frame of his agitator is made from 5 and 6-in schedule 40 pipe along with 3-in channel iron The rig is 10 ft wide 20 ft long and weighs about 14 000 lbs The engine and fuel tank are mounted in the middle The pumps are mounted fore and aft on swivel joints from old cement trucks Flotation tanks on each side are filled with styrofoam His rig is powered by an L10 Cummins diesel engine that produces 310 hp Lindstrom and his crew removed it from an old concrtete mixing truck and overhauled it before re-assembling it on the agitator frame Lindstrom used his custom-built agitator boat about 400 hrs during the 2013 pumping season and considered the project very successful “I can stir up an 8 million gal pit in 8 hrs ” he says “The hydro power lets me turn the agitator in a circle thrust sidewise fore and aft and rotate 180 degrees to disintigrate a crust or dislodge materials on the bottom The pumps output 2 500 gals per minute at about 45 lbs psi through 3 and 3 1/2-in lines ” The agitator has another very unique feature Lindstrom says he can remove a nozzle from one of the pumps attach a hose and feed slurry into a vehicle on the side of the pit Large tankers are filled in about 3 min Lindstrom uses a process control computer to run the machine It reads pressure on the lines and at the engine then sends electronic signals through solenoids to actuators that run controls on the hydrostat Valves are proportional to accept a pulse-less signal from the solenoid Speed is adjusted by pressing and holding or releasing buttons on the remote actuator The left-right action of the pump heads is controlled by hydraulic cylinders and the fore-aft movement with a chain and sprocket “Running the agitator is like playing a video game ” says Lindstrom “I’m okay running it but a 13 or 14 year-old kid who grew up on video games would be fantastic It’s just a matter of tapping buttons to thrust the boat control speed and direction ” Lindstrom isn’t sure how many hours it took to build the machine or what the cost is but he’s quick to say “I know it’s a lot less than buying one of those on the market It was worth every penny because it saves us the use of several tractors and portable pumps ” Contact: FARM SHOW Followup Chris Lindstrom Maxville Truck & Repair S460 State Road 25 Durand Wis 54736 ph 715 672-7867
To read the rest of this story, download this issue below or click
here to register with your account number.