You have reached your limit of 3 free stories. A story preview is shown instead.
To view more stories
(If your subscription is current,
click here to Login or Register.)
Jibs Make Light Work Of Heavy Lifting
“They work great to lift heavy parts and equipment,” says Andy Hall, who operates an on-farm repair and welding shop on his family’s farm near Butterfield, Minn. “When we put up a big new shop, the first thing we did was build several jibs like we had in our old shop. I use one of them in the welding shop, my brothers
..........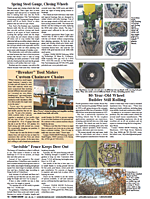
You must sign in, subscribe or renew to see the page.
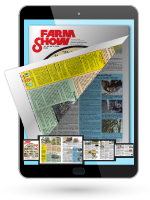
You must sign in, subscribe or renew to see the flip-book
Jibs Make Light Work Of Heavy Lifting FARM SHOP Maintenance “They work great to lift heavy parts and equipment ” says Andy Hall who operates an on-farm repair and welding shop on his family’s farm near Butterfield Minn “When we put up a big new shop the first thing we did was build several jibs like we had in our old shop I use one of them in the welding shop my brothers Mike and Tony have 5 in their machine shop and we’ve got another one in the service bay where we work on cars trucks and tractors ” The jibs are strategically located throughout four service areas in the 10 000 sq ft building The horizontal arms rotate smoothly on 8-bolt heavy-duty wheel hubs bolted onto the top of vertical posts They’re positioned to lift and move heavy parts anywhere in the building yet not interfere with door frames ceiling fans or another jib “We drew up everything to scale on paper before the floor was poured ” says Andy “and everything worked perfect once they were all in place ” Four of the jibs are the exact same design with each leg made of 13-in dia by 1/2-in tube steel Those legs hold a 10-in by 6-in I-beam used for the horizontal arm A 6-ft support brace is made from 5 by 7-in tubing The large jibs are 14 ft tall Two other jibs are the same design but use a smaller I-beam because they lift lighter parts in Tony’s performance machining shop Mike uses a shorter 8-ft jib in the room that houses his turning lathe The base for each of the jibs is a 36-in dia plate that’s bolted solidly to the concrete floor with six 3/4-in machine bolts Six gussets welded to the plate and to each vertical leg provide lateral support in every direction Each jib has a 1 300-lb electric hoist that rides on its horizontal I-beam The hoists are equipped with a 1 1/2-hp motor and a tethered remote so the brothers can lift and move heavy parts anywhere in the shop The brothers agree that having several jibs located throughout the shop allows each of them to work independently and not always ask for help anytime something is too heavy to lift by hand All of the jibs are painted bright red giving the appearance of giant cranes hovering over tall buildings They stand out against the white interior shop walls The jibs cost about $500 apiece for materials and took about 8 hrs to build “They save us a lot of time and let us move heavy parts and pieces anywhere in the shops ” says Andy Contact: FARM SHOW Followup Andy Hall 40133 620th Ave Butterfield Minn 56120 ph 507 956-2020
To read the rest of this story, download this issue below or click
here to register with your account number.