You have reached your limit of 3 free stories. A story preview is shown instead.
To view more stories
(If your subscription is current,
click here to Login or Register.)
16-Row Stack Planter Works Great
“I built this 16-row stack planter using parts from three individual planters and a lot of extra scrap iron,” says Brian Hoogestraat, who raises corn and soybeans with his father near Chancellor, S. Dak. He started the project with two Deere 7200’s and the frame off an International 800 mounted planter.
“First
..........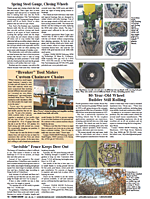
You must sign in, subscribe or renew to see the page.
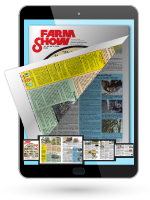
You must sign in, subscribe or renew to see the flip-book
16-Row Stack Planter Works Great PLANTERS “I built this 16-row stack planter using parts from three individual planters and a lot of extra scrap iron ” says Brian Hoogestraat who raises corn and soybeans with his father near Chancellor S Dak He started the project with two Deere 7200’s and the frame off an International 800 mounted planter “First I pulled off all the row units to strip the planters down to their main frames ” Hoogestraat says “Then I removed the hitches from the Deere planters and spent a lot of time thinking about how to put everything back together ” The center section of his rig uses the original IH 800 frame the hitch mechanism and the lift assist wheels He doubled the 7 by 7-in main frame to provide the extra strength needed to support the four rows on each wing He put 4-in spacers between the two bars to provide lateral support Hoogestraat cut almost a 10-ft long piece from the main bar of each 7200 frame to make the bar for each wing He welded brackets on one end of each piece so they would slide into a sleeve on each end of the center section Then he built wing lift brackets to mount a 4 by 24-in dual acting cylinder The cylinders lift the wings from underneath and raise them above the center frame supported by a pivoting brace made of tubing The 4th row unit in from the outside on each wing raises slightly as the wings are lifted The wings pivot on greasable pins “My design is real simple and the wings actually stack tighter and transport lower than commercial units on the market ” Hoogestraat says “The markers are about a foot above the boxes when the wings are folded but the overall height easily fits in our shed ” The planter is fitted with 16 row units from the 7200 Deere planters They’re powered by a 7200 ground drive system that Hoogestraat re-configured for his rig “When the wings are down I set the cylinders on float and the planter follows the ground contour real well ” Hoogestraat says The weight of the bar and row units provides plenty of down pressure for consistent planting depth “The best part is that I can raise the wings on this planter to get through a wet spot and not have to worry about bogging the whole thing down ” says Hoogestraat “That’s not possible with a toolbar type planter that folds forward ” Hoogestraat figures he spent about $15 000 to configure and build his custom-made planter “It took me the better part of a couple months over one winter ” he says “If we were to buy this machine from a dealer the cost might have been $70 000 to $80 000 maybe more ” Hoogestraat pulls the stackable planter with an IH 7130 MFWD Magnum and says the machine has worked great the past five years Contact: FARM SHOW Followup Brian Hoogestraat 27515 464th Ave Chancellor S Dak 57015 bhoggy@hotmail com
To read the rest of this story, download this issue below or click
here to register with your account number.