They're Using Compost To Heat Their Homes
Instead of burning wood for heat, some Europeans now build a compost pile over plastic water lines that extract heat from the decomposing plant material. Temperatures can get as high as 149 degrees. With a circulating pump as the only moving part, the compost heater lasts an average of 12 to 16 mos. – and occasionally up to 24 mos. – providing heat and up to 80 percent of the hot water for a 1,500 sq. ft. home.
Homeowners interested in compost heat attend seminars to learn the method, says Heiner Cuhls, who conducts workshops through his business, Native Power. So far, he has helped set up 25 systems.
Typical compost mounds are 16 ft. in diameter and 8 ft. tall. The primary plant material is deciduous brush and scrub wood chipped no finer than 1 1/2 by 1/2-in. Only about 15 percent can be pine, since the needles and wax are too sour for the microbes to digest in the compost process.
The materials required are basic: 1,300 to 3,500 cubic ft. of shredded green wood, heat exchange pipe, a pump and construction steel fencing or galvanized steel fencing. Once the wood is shredded, it can take as few as 6 hrs. to build with a skid steer or tractor loader.
There are a few design options, but they all have common elements. First, heavy black plastic (used in ponds) is spread on the ground to prevent tannic acid from concentrating and seeping into the ground water. The plastic also holds the water during the first four days of watering to prevent the bacteria needed for composting from washing away.
Next comes a layer of chipped wood, topped by pipe in concentric circles, plastic-tied on construction steel to stay in form. Repeat the process for four layers of pipe and five layers of chipped wood. Wood chips are heaped up inside upright steel fencing.
Another design wraps the water lines around upright fencing and piles the wood inside and outside to bury the water lines. Finally, an even simpler version uses chipped wood in sacks. Eight men can fill and stack 1,000 sacks for a 1,300 cu. ft. compost heater in about 6 hrs., Cuhls says.
He emphasized a few points. First, the wood must be green and not chipped too small, because small chips pack too tight to let in enough oxygen to compost.
“The second secret of success is to water the green cut for the first four days, so that it’s well soaked and at up to 70 percent moisture. As much as 8,000 gal. of water will be used,” Cuhls says. “The most common mistake is not enough water and wood that’s not green enough.”
The beauty of the system is that the materials (fencing and pipes) can be reused for 10 to 15 years if the compost pile is carefully disassembled. And, Cuhls adds, after the heat is out of the compost it makes good fertilizer.
Colder climates require bigger compost heaps. If the pile is too small, the temperature of the heap might fall when the outside temperatures drop.
In the U.S., where hot air systems are more common, you can use 5-in. dia. plastic drain tile to carry hot air into the house.
Prices for the initial investment of materials in the U.S. run between $800 to $1,500, Cuhls estimates, based on material for air circulation systems.
For more information, check out his Native Power website, which includes videos of the building process.
Contact: FARM SHOW Followup, Heiner Cuhls, Native Power Ltd., 88 Hurstbourne Rd., London, SE23 2AQ, United Kingdom (ph 0049 152 51 400 400; www.native-power.de).
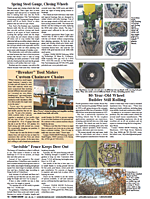
Click here to download page story appeared in.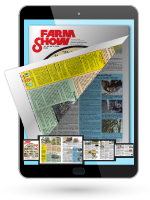
Click here to read entire issue
They re Using Compost To Heat Their Homes BUILDINGS Houses Instead of burning wood for heat some Europeans now build a compost pile over plastic water lines that extract heat from the decomposing plant material Temperatures can get as high as 149 degrees With a circulating pump as the only moving part the compost heater lasts an average of 12 to 16 mos – and occasionally up to 24 mos – providing heat and up to 80 percent of the hot water for a 1 500 sq ft home Homeowners interested in compost heat attend seminars to learn the method says Heiner Cuhls who conducts workshops through his business Native Power So far he has helped set up 25 systems Typical compost mounds are 16 ft in diameter and 8 ft tall The primary plant material is deciduous brush and scrub wood chipped no finer than 1 1/2 by 1/2-in Only about 15 percent can be pine since the needles and wax are too sour for the microbes to digest in the compost process The materials required are basic: 1 300 to 3 500 cubic ft of shredded green wood heat exchange pipe a pump and construction steel fencing or galvanized steel fencing Once the wood is shredded it can take as few as 6 hrs to build with a skid steer or tractor loader There are a few design options but they all have common elements First heavy black plastic used in ponds is spread on the ground to prevent tannic acid from concentrating and seeping into the ground water The plastic also holds the water during the first four days of watering to prevent the bacteria needed for composting from washing away Next comes a layer of chipped wood topped by pipe in concentric circles plastic-tied on construction steel to stay in form Repeat the process for four layers of pipe and five layers of chipped wood Wood chips are heaped up inside upright steel fencing Another design wraps the water lines around upright fencing and piles the wood inside and outside to bury the water lines Finally an even simpler version uses chipped wood in sacks Eight men can fill and stack 1 000 sacks for a 1 300 cu ft compost heater in about 6 hrs Cuhls says He emphasized a few points First the wood must be green and not chipped too small because small chips pack too tight to let in enough oxygen to compost “The second secret of success is to water the green cut for the first four days so that it’s well soaked and at up to 70 percent moisture As much as 8 000 gal of water will be used ” Cuhls says “The most common mistake is not enough water and wood that’s not green enough ” The beauty of the system is that the materials fencing and pipes can be reused for 10 to 15 years if the compost pile is carefully disassembled And Cuhls adds after the heat is out of the compost it makes good fertilizer Colder climates require bigger compost heaps If the pile is too small the temperature of the heap might fall when the outside temperatures drop In the U S where hot air systems are more common you can use 5-in dia plastic drain tile to carry hot air into the house Prices for the initial investment of materials in the U S run between $800 to $1 500 Cuhls estimates based on material for air circulation systems For more information check out his Native Power website which includes videos of the building process Contact: FARM SHOW Followup Heiner Cuhls Native Power Ltd 88 Hurstbourne Rd London SE23 2AQ United Kingdom ph 0049 152 51 400 400; www native-power de
To read the rest of this story, download this issue below or click
here to register with your account number.