You have reached your limit of 3 free stories. A story preview is shown instead.
To view more stories
(If your subscription is current,
click here to Login or Register.)
Combine Converted To Front-End Loader
Val Siddoway of Laketown, Utah runs a cow-calf operation and grows lots of hay. To load bales onto trucks, he converted an IH 815 hydrostatic combine into a bale fork-equipped loader that can pick up and stack 10 small square bales at a time.
"I built it because I couldn't justify the cost of a new loader tr
..........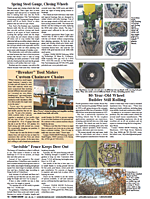
You must sign in, subscribe or renew to see the page.
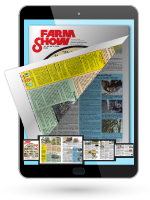
You must sign in, subscribe or renew to see the flip-book
Combine Converted To Front-End Loader BALE HANDLING Bale Handling 31B Val Siddoway of Laketown Utah runs a cow-calf operation and grows lots of hay To load bales onto trucks he converted an IH 815 hydrostatic combine into a bale fork-equipped loader that can pick up and stack 10 small square bales at a time I built it because I couldn t justify the cost of a new loader tractor says Siddoway I used mostly salvaged materials to build it My total cost was less than $2 000 I drop the bales on the ground behind the baler and later use a self-propelled New Holland bale wagon to pick them up and unload the bales in stacks During the winter I use the combine hay loader to load the bales from the stacks onto a truck - an old World War II 2 1/2-ton 6-WD army truck û for feeding on pasture He got the combine from a neighbor and removed the threshing parts leaving the engine cab transmission and running gear intact He used 8-in channel iron to reinforce the combine s frame Then he repositioned the cab and engine to make room for the bale fork The cab originally offset to the side was remounted to the center of the machine The engine which originally sat on top of the combine along with the hydrostatic drive and hydraulic pump was remounted on back Then he bought an old heavy-duty front-end loader at a salvage yard and welded in new material to lengthen it by 2 ft so that it would raise high enough to load bales onto trucks To build the bale fork he copied a commercial model but made it much heavier I m in the repair business and over the years I ve had to fix way too many bale forks because they were built too light says Siddoway He used 4-in steel tubing to build the shafts that support the teeth which he bought from a New Holland dealer The teeth are arranged in 4 rows and are spaced 1 ft apart The bale fork is attached to a large rectangular steel plate that pins onto the loader arms By activating a hydraulic cylinder the entire bale fork can be rotated 90 degrees to the left or right Siddoway cut the track-rotating mechanism off an old World War II Japanese army tank and welded it to the center of the bale fork where a hydraulic cylinder rotates the bale fork I wanted a rotating bale fork because I stack bales on the truck lengthwise and crosswise in alternate layers explains Siddoway With a conventional bale fork I would have to change directions with the loader I can pick up a load of hay back up to the truck and then rotate the fork so I don t have to turn around all the time The bale fork s teeth are opened and closed by a single hydraulic cylinder Another cylinder tilts the bale fork up or down and another raises and lowers the loader He says the bale fork has twice as many teeth as most commercial models so it s sure to pick up all the bales On most commercial bale forks the teeth are spaced farther apart and don t always grab the bales securely The loader is raised and lowered by a pair of 4-in hydraulic cylinders It s built much heavier than conventional loaders After repairing a lot of loaders over the years I knew I wanted something heavy says Siddoway The combine came equipped with diamond tread tires on front I like that the tires don t leave deep ruts in the ground However they also don t have much traction so I installed chains on the drive tires which really help when it s wet says Siddoway who also added wheel weights on back of the rig and filled the tires with fluid Contact: FARM SHOW Followup Val Siddoway Falula Farms Inc P O Box 57 Laketown Utah 84038 ph 435 946-3321
To read the rest of this story, download this issue below or click
here to register with your account number.