You have reached your limit of 3 free stories. A story preview is shown instead.
To view more stories
(If your subscription is current,
click here to Login or Register.)
He Grinds Stumps With Circular Saw Blades
"I had several large tree stumps in my yard that had to be removed. I didn't want to spend the money to have the work done so I made my own 3-pt. mounted stump grinder mostly out of scrap material," says Donald Johnson, Maryville, Tenn.
Johnson uses the stump grinder on his Cub Cadet 24 hp tractor. Power is prov
..........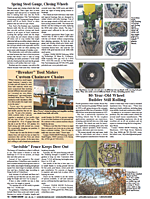
You must sign in, subscribe or renew to see the page.
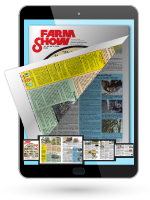
You must sign in, subscribe or renew to see the flip-book
He Grinds Stumps With Circular Saw Blades WOODLOT EQUIPMENT Stump Cutters 33-4-26 "I had several large tree stumps in my yard that had to be removed. I didn't want to spend the money to have the work done so I made my own 3-pt. mounted stump grinder mostly out of scrap material," says Donald Johnson, Maryville, Tenn.
Johnson uses the stump grinder on his Cub Cadet 24 hp tractor. Power is provided by a 6 1/2 hp Briggs and Stratton engine that belt-drives the grinder. The grinder itself consists of four 10-in. dia. circular saw blades (24-tooth, carbide-tipped) with spacers between them. The entire unit mounts on an angle iron frame. The bottom part of the frame is pinned to the 3-pt.'s lower lift arms, while the top part is connected to a metal arm extending back from the 3-pt.'s top link.
The stump grinder is designed so it can be swung up to 12 in. from side to side across the stump, using the flexibility provided by loosening the sway chains on the 3-pt.'s lower lift arms. The operator grabs a T-bar handle to guide the unit. A trip lever mounts on the handle and is connected by a length of cable to a ratchet dog, which locks onto a vertical metal post. Pulling the trip lever back releases the ratchet dog from the post, allowing the operator to lower the grinder into the stump.
Heavy duty bunge cords extend from the tractor back to the frame to counterbalance the weight of the grinder, making it easier for the operator to lift.
"I've used this stump grinder for three years and have removed more than 50 stumps. It works great," says Johnson. "I use the 3-pt. to lower the grinder to within 4 in. of the stump, then get off the tractor and use the trip lever to lower the grinder into the stump. If the stump is wider than 12 in. the tractor has to be repositioned after each cut across the stump. The grinder cuts a path only about 3 in. from front to back, so I also may have to back up the tractor several times, depending on the size of the stump."
"I've gone through four or five sets of blades since I made it, but I've never had to reweld anything on it. At first I used welded-together steel pulleys which came apart, so I replaced them with cast iron pulleys. I use a big threaded bolt to adjust tension on the belt.
"I bought the motor, pulleys, belt and blades for about $400. Everything else that I used, I already had."
Contact: FARM SHOW Followup, Donald E. Johnson, 250 Cedar Pointe Ln, Maryville, Tenn. 37801 (ph 865 856-0142).
To read the rest of this story, download this issue below or click
here to register with your account number.