You have reached your limit of 3 free stories. A story preview is shown instead.
To view more stories
(If your subscription is current,
click here to Login or Register.)
Farmall M Gets Heavy Duty 3-Pt.
Wayne McKenzie liked his Farmall M, but he liked it even better after he rigged it up with a 3-pt. hitch. The homemade lift is heavy duty from top to bottom.
"I can pick up loads that will lift the front wheels off the ground," says McKenzie.
The retired postman fabricated each component of t
..........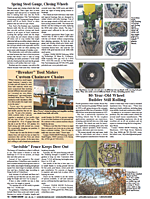
You must sign in, subscribe or renew to see the page.
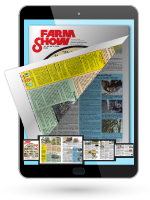
You must sign in, subscribe or renew to see the flip-book
Farmall M Gets Heavy Duty 3-Pt HITCHES Hitches Wayne McKenzie liked his Farmall M but he liked it even better after he rigged it up with a 3-pt hitch The homemade lift is heavy duty from top to bottom
I can pick up loads that will lift the front wheels off the ground says McKenzie
The retired postman fabricated each component of the 3-pt except for the lift cylinders and the top link arm To anchor the 3-pt to the tractor he fastened steel plates each made from four pieces of angle iron to either side of the rear axle using U-bolts These plates serve as the base to attach the lower arms
McKenzie installed a steel plate under the differential attaching it to the bottom inside corners of each axle plate This plate serves as a base for the two hydraulic cylinders that raise and lower the upper arms
The bolts that connect each side of the base plate to the axle plates also run through two steel uprights bolted to the differential housing and through the swivel ball ends of the lower arms
The steel uprights are cut and drilled to match the axle housing where it bolts to the differential Housing bolts go through the uprights and then through the axle housing to the differential housing
A 4 by 6-in angle iron extends across the two uprights and bolts to both Bearings for a 2 1/4-in shaft that had once served to lift a header on a one-row cotton picker were bolted to the angle iron At the center point of the angle iron two pieces of steel were welded in place to serve as an anchor clevis for the top link arm
The shaft serves as a pivot point for the upper arms that raise and lower the lower arms These upper arms had to be especially heavy duty to take the pressure of the two hydraulic cylinders that would provide the lift
These upper arms also had to be fabricated to translate the hydraulic cylinder s 8-in extension into a desired 32-in lift height for the tips of the lower arms
I built the upper arms out of lengths of 1 by 3-in steel plate says McKenzie Each arm had two short plates with holes drilled in one end to fit over the pivot shaft The other ends were cut at an angle to match angled ends of two longer plates that were boxed at the other end
Welded together the arms formed an angle of about 30 degrees Once in position on the shaft he welded them in place A short piece of reinforcing steel plate was also welded into place just past the point at which each arm angled downward
McKenzie welded a short length of plate with three holes in it to the inside of each arm just below the reinforcing plate These serve as connection points for the lift cylinder clevis A similar four-holed plate is welded to the outside plate of each arm at its boxed end while a 3-holed plate is welded to the top of the lower lift arms
McKenzie fabricated two adjustable lift arms to connect the upper lift arms and lower lift arms One lift arm consisted of two clevis ends and a center rod The other was a leveling arm using clevis ends and threaded rod
I can adjust how much I can lift or lower the tips of the lower arms and how much weight I can lift by adjusting which holes the various clevis are pinned to explains McKenzie
Contact: FARM SHOW Followup Wayne McKenzie P O Box 66 Parma Mo 63870 ph 573 357-4435 after 5 p m or 573 281-6015 daytime
To read the rest of this story, download this issue below or click
here to register with your account number.