You have reached your limit of 3 free stories. A story preview is shown instead.
To view more stories
(If your subscription is current,
click here to Login or Register.)
Build Yourself A Self-Propelled Chopper
"It'll chop 5 tons of silage in three minutes," says Jack Janssen, Scipio Center, N.Y., who along with his brother Rick and engineering student Stef McGonagle, who worked for them, turned two 3-row Hesston choppers around and mounted them on the front of a 320 hp. Steiger tractor.
The turned-around choppers moun
..........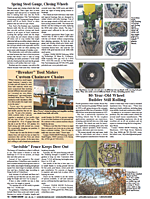
You must sign in, subscribe or renew to see the page.
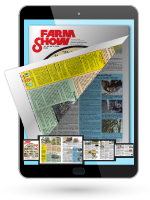
You must sign in, subscribe or renew to see the flip-book
Build Yourself A Self-Propelled Chopper FORAGE HARVESTERS Forage Harvesters (31F) 7-3-4 "It'll chop 5 tons of silage in three minutes," says Jack Janssen, Scipio Center, N.Y., who along with his brother Rick and engineering student Stef McGonagle, who worked for them, turned two 3-row Hesston choppers around and mounted them on the front of a 320 hp. Steiger tractor.
The turned-around choppers mount on a heavy-duty frame and are powered by a specially-rigged pto that's driven directly off the crankshaft. Articulated, 4-WD power gives the tractor the power and maneuverability to out-perform and out-maneuver any other commercial forage harvester on the market, according to Janssen.
"In muddy ground, pull-behind choppers often slip, knocking over more corn than they harvest while self-propelled choppers often don't have enough power and overheat or strain in adverse conditions. But with the Steiger we always have power to spare. And, it gives us another use for an expensive tractor which might otherwise sit idle through harvest," says Janssen.
Janssen says he first had the idea for the "perfect" forage harvester years ago but didn't start building it until about 3 years ago. It has been used successfully for two full seasons.
The Janssens started with two identical used Hesston pull-behind 3-row choppers. The pto shaft, 90? gearbox, tires and excess framework were stripped off the choppers. "We picked the Hesston because we already had one and because the blower is directly behind the cutterhead, which made it easier to mount it close to the front of the tractor," points out Janssen, noting that other models would, however, work for the conversion.
The next step was to build a sub-frame to hold the choppers. The frame bolts to the Steiger frame and could be used, when the choppers are not in use, to hold a dozer blade, spray tanks or other equipment.
To power the choppers, the men brought a shaft directly off the crankshaft, running it through the steel radiator housing ù not through the core ù and through the hydraulic reservoir. A drive belt runs to a gear-box directly below the shaft and three output shafts ù one to each cutterhead and the third to the blowersù carry the power to the choppers. "This gearbox was our biggest problem," notes Janssen. "We finally found a company ù Safeguard Technical Systems in Aberdeen, S. Dak. ù that makes just what we needed."
About the only modification to the choppers, besides stripping them of all non-essential framework, involved shifting the cutterhead driveshaft on one unit from the outside to the center and extending the blower tubes to reach behind the tractor. It takes two men 2 to 3 hrs. to mount the chopper. Janssen says that if Steiger had a front pto it could be made to quick-tach.
The only real problem in operating the Steiger-mounted chopper is crossing ditches and hills because it can't be pivoted up and out of the way. The inventors plan to solve the problem with their next front-mounted chopper by using two Deere 4-row heads that not only pivot but will float independently of each other.
At recent farm shows, the Janssens have worked through fields alongside commercial 6-row self-propelled choppers and say that their machine easily held its own against the others. "One of the strong points of using a big 4-WD tractor is that it has enough power so that the equipment never has to strain. There's less breakage," he notes.
The chopper has been in use on the Janssen farm for the last two seasons and, in addition to taking care of their own large needs, they have had excess silage to sell each of the last two years.
The machine has been so successful that a manufacturer ù Crary Company, Box 1779, Fargo, N. Dak. 58107 (ph 701 282-5520) ù plans to introduce a front-mounted chopper, or kits to convert your existing pull-type chopper, for 4-WD's this summer. According to Dave Majkrzak, company vice president, the first two prototypes are scheduled to be delivered this spring. The two choppers feature a major manufacturer's 4-row header, chopper box and fan. Crary is now taking or
To read the rest of this story, download this issue below or click
here to register with your account number.