1990 - Volume #14, Issue #1, Page #03
[ Sample Stories From This Issue | List of All Stories In This Issue | Print this story
| Read this issue]
Add On Tractor Pushes Combine Through Mud
![]() |
![]() |
The tow-behind tractor in effect replaces the combine's rear axle. A home-built draw-bar made out of a 7-ft. long, 4-in. dia. double strength oil well pipe hitches the tractor to the combine. One end of the pipe is welded to a2-ft. long vertical steel post (1-in. thick sidewalls) that's welded to the tractor draw-bar. A 2-ft. long, 2-in. dia. pin inside the post acts as a pivot point and allows a hydraulic cylinder mounted behind the tractor to steer the combine. The other end of the hitch pipe is bolted to the combine frame-work that originally connected the front and rear axles. A pair of cables and a pair of hydraulic hoses running from the combine cab to the tractor control steering, as well as the tractor's clutch and throttle.
"It was so wet in our area in the fall of 1984 that we couldn't get crops out with our 2-WD combine," says Greer. "Some farmˇers bought $2,000 Mud Hog-type drive systems for their combines, but I didn't want to spend the money. I got the idea watching some earth-moving construction equipment. It works well because the weight of the tractor perfectly counterbalances the weight of the combine so the midpoint is right at the pivot point, which is 2 ft. behind the tractor axle. The balance is so near perfect that I don't even need front wheels on the tractor, which would only get stuck in the mud anyway. The tractor's rear wheels are only 3 ft. behind the original location of the combine's rear axle. If the tractor faced forward its rear wheels would be so far from the combine that it would require huge I-beams to carry the combine's weight.
"Extending or retracting the hydraulic cylinder at the pivot post steers the combine the same way articulated steering controls a 4-WD tractor. A pair of hydraulic hoses, which originally operated the combine's hydraulic steering cylinder, controls moveˇment of hydraulic cylinder at the pivot post. Retracting the hydraulic cylinder causes the tractor to slide right and the combine to go
left. Extending the cylinder causes the tracˇtor to turn left and the combine to go right," notes Greer. "I can turn just as short as with a conventional combine, but I can't back up without getting off the combine and putting the tractor in reverse."
To go to the field, Greer starts the tractor and disengages its clutch, then hops into the combine cab. To get started, he engages the combine clutch and then the tractor clutch and opens up its throttle from the combine cab. Chains on the tractor wheels provide extra traction. "The only time I ever got stuck was when I plugged the combine cylinder and had to stop before I could disengage the tractor clutch," says Greer. "The tractor killed and when I started the combine up again I was stuck."
Greer reversed the transmission by turnˇing over the pinion gears. "At first I operated the tractor in reverse gear but it didn't go fast enough. Turning the pinion gears over gives the tractor four gears in reverse. One problem is that the switch changed the position of the shifting forks from the left side of the tractor to the right side, which meant I needed a different transmission cover. I solved the problem by installing a transmission cover designed for an International cotton picker with forks on the right side. I run the tractor in second gear which matches low gear on the combine."
Greer enclosed the 3/8-in. clutch and throttle cables inside a pair of 1/2-in. dia. plastic pipes which run from the combine cab to the tractor. A 5-in. stroke hydraulic cylinder is mounted on top of the tractor's transmission and pushes against the clutch. "Whenever I pull the clutch cable, it pulls a hydraulic lever on the tractor which extends the hydraulic cylinder to disengage the clutch lever," explains Greer.
To brace the pivot point, Greer bolted a pair of 3 by 3 1/2-
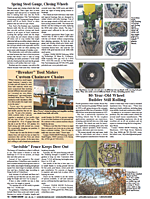
Click here to download page story appeared in.
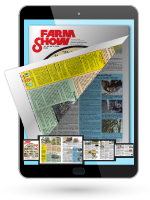
Click here to read entire issue
To read the rest of this story, download this issue below or click here to register with your account number.