2003 - Volume #27, Issue #2, Page #33
[ Sample Stories From This Issue | List of All Stories In This Issue | Print this story
| Read this issue]
Home-Built Hydraulic Rock Rake
![]() |
![]() |
"I wanted a pull-type rake because I felt it would do a better job if it were mounted on wheels that were running over the ground you just de-rocked and smoothed, rather than moving up and down with the tractor from the rough terrain," he says.
Daus does a lot of shop work so he decided to make what he needed to.
With the help of a friend, he put together an all-hydraulic side delivery rock rake that can be angled to windrow rocks to either side.
He made the rotor of 6-in. dia., 5/16-in. walled pipe, with 3/4-in. sq. solid steel bars wrapped at an angle around the outside of it. The bars sift and winnow the rocks. He says twisting the bar around the pipe, so the whole sifter bar is not in contact with the ground at one time, prevents excess bouncing
They mounted the rotor in a frame using 1/2-in. plate steel for the sides and 1/4-in. plate for the rest. A piece of 8-in. I-beam was used to make an arching tongue, and for wheels they used an axle designed for a 3,000-lb. trailer.
The rotor is chain-driven by a hydraulic motor. "Powering the rotating drum with hydraulics is much better than with a pto because if the drum gets a rock jammed in it, the hydraulics will stall rather than brake a shear pin or worse. And I can just reverse the motor to back off the drum and release the jammed rock," he says.
Hydraulic cylinders control the angle of the rotor and height of the sifter by raising or lowering the rear-mounted wheels.
Although he bought the trailer axle and hydraulic motor new and had the hoses made at a local shop, he was still able to put the entire machine together for under $800. "That's less than 25 percent of the cost of the commercial three point machines and I think mine does a better job," he says.
"My buddy and I put in about 35 hours in the shop, total," he adds. "The most difficult part was bending the steel bar and welding it onto the pipe to make the sifter rotor."
Contact: FARM SHOW Followup, Chuck Daus, Ickes Heights Road, Imler, Penn. 16655 (E-mail: dauscj@nb.net).
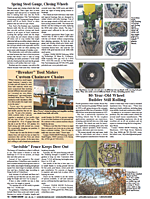
Click here to download page story appeared in.
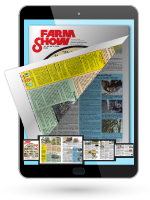
Click here to read entire issue
To read the rest of this story, download this issue below or click here to register with your account number.