2005 - Volume #29, Issue #3, Page #38
[ Sample Stories From This Issue | List of All Stories In This Issue | Print this story
| Read this issue]
Heavy Duty Shop Hoist Made From Old Disk Gangs
![]() |
"All I used was scrap metal, so it cost almost nothing to build," says Vickers.
The hydraulic-operated hoist has an upper hinged "floor" that folds down flat. The floor moves forward and upward at the same time.
He started with an 18-ft. Deere tandem disk and cut off the wings, keeping only the 4 by 4-in. hinged frame members that allowed the wings to fold up. He pinned the frame members together so there are four hinges on each side. He also welded material in between the two sides. The floor measures 4 ft. wide by 5 ft. long and is raised or lowered by a 4-in. hydraulic cylinder attached to a pair of metal legs. The cylinder is operated by a pump that's belt-driven by an electric motor.
The motor and pump, as well as a hydraulic reservoir, mount together on a metal "sled" next to the hoist. To raise or lower the hoist, Vickers simply operates a valve on the pump.
"It works great. It raises and lowers slowly but that's what you want for safety," says Vickers. "The cylinder is off an old wagon and the pump off a combine. My only cost was for welding rod. I use it with my 20 hp riding mower. I just drive the mower onto the platform, raise it up, and go to work. Once the mower is up in place I remove a steel plate from the floor, which gives me full access to the underside of the mower."
Contact: FARM SHOW Followup, Robert J. Vickers, 561 Shelby 400, Clarence, Mo. 63437 (ph 660 699-3522).
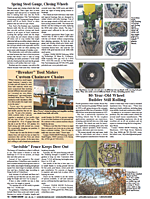
Click here to download page story appeared in.
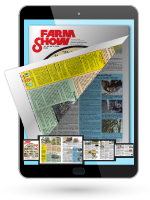
Click here to read entire issue
To read the rest of this story, download this issue below or click here to register with your account number.