You have reached your limit of 3 free stories. A story preview is shown instead.
To view more stories
(If your subscription is current,
click here to Login or Register.)
Home-Built 24-Row, 15-In. No-Till Planter Made From Two IH Planters
Brian Parkinson says there were several factors that caused him to build his own 24-row, 15-in. no-till air planter from a variety of planter components.
He wanted more exact and better seed placement, especially when using Roundup Ready seed.
He could not justify new equipment. A new 24-ro
..........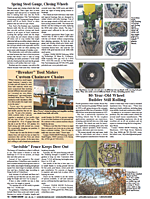
You must sign in, subscribe or renew to see the page.
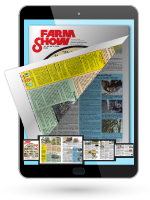
You must sign in, subscribe or renew to see the flip-book
Home-Built 24-Row, 15-In. No-Till Planter Made From Two IH Planters PLANTERS Planters 25-6-32 Brian Parkinson says there were several factors that caused him to build his own 24-row, 15-in. no-till air planter from a variety of planter components.
He wanted more exact and better seed placement, especially when using Roundup Ready seed.
He could not justify new equipment. A new 24-row, 15-in. planter would cost well over $50,000.
There was a ready supply of older IH Cyclo planters available at low cost.
"We combined two IH 12 by 30-in. vertical fold planters, tying them together front to back with 5 by 7-in. box beams.
"One of the planters came with a Progressive Farm Equipment caddy so I use the planter as a pull-type, although it may be possible to use the planter as a 3-pt. with lift assist if the caddy was removed. I use my Deere 8440 4-WD tractor to pull it.
"Before I built it I visited other farmers who had built their own planters. In addition, I traded ideas and even bought and sold parts for the planter over the Internet. I paid $7,500 for the two planters and miscellaneous used parts from Cyclo 400, 500, and 900 planters. My total cost, including a Rawson hydraulic drive system, was about $14,000 so I saved a lot of money."
Parkinson elevated the seed boxes 12 in., mounting them on a 4-in. sq. box beam to allow more room for the seed tubes and drum drive assemblies. Two seed boxes mount on the rear planter bar, and one is center-mounted on the front bar. The three boxes hold a total of about 45 bu. of seed. Catwalks allow easy access to both bars as well as to the area between them. A refurbished Rawson hydraulic drive unit drives the original primary driveshaft through the original seed transmission. Transmission power is sent to the back bar via a long no. 50 chain to a jackshaft, then up to the two rear-mounted seed hoppers.
The original pto-powered hydraulic pump that powered the seed blowers was too small, so he replaced it with a larger pump. The pump mounts on the tractor drawbar and is connected to the pto by a short shaft. The original planter markers and controls are attached to the front bar. Parkinson doubled up on the front stationary wheel depth assemblies and tied them together in pairs with a 2 by 4-in. tube in order to keep them from twisting. He also doubled up the tubes for the rear lift assist assemblies and replaced the original IH castor wheels with much heavier Flexi-Coil castor wheels. Four hydraulic cylinders are used to power the lift assist wheels.
In planting position, the planter's rear wings are carried by shortened lift assist assemblies. There are no hydraulic cylinders on the assemblies, just screw jacks. The original planters automatically lifted the wings slightly whenever the planters were raised for turning in order to keep the wings from dragging. Adjustments for planting depth and other functions are the same as on the original planters. And, the planter folds just as the original planters did. Parkinson added tractor weights to each rear wing as needed.
"I use the Deere 250 seed monitor from my Deere 7200 12-row planter," says Parkinson. "I had a harness custom made by Ag Express to merge the two original 12 by 30-in. harnesses into one harness that plugs into my Deere monitor. The Rawson hydraulic drive system is hooked up to the radar gun on the Deere monitor via a æY' cable."
Contact: FARM SHOW Followup, Brian Parkinson, 16619 56th St. W., Milan, Ill. 61264 (ph 309 372-8263 or 309 737-4579; E-mail: parkwb@winco.net).
To read the rest of this story, download this issue below or click
here to register with your account number.