You have reached your limit of 3 free stories. A story preview is shown instead.
To view more stories
To view more stories
SUBSCRIBE OR RENEW NOW
(If your subscription is current, click here to Login or Register.)1980 - Volume #4, Issue #4, Page #27
[ Sample Stories From This Issue | List of All Stories In This Issue]
New Slant On Milk, Manure Handling
Paul Longacre's new stall barn near Coopersburg, Lehigh County, Penn., looks conventional enough from the outside. But inside there's a startling difference - the floor is on a tilt. It slopes."By sloping the barn floor we've been able to utilize gravity flow for both milk and manure," Paul explains.
"As a..........
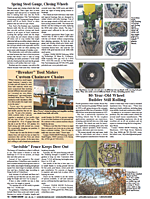
You must sign in, subscribe or renew to see the page.
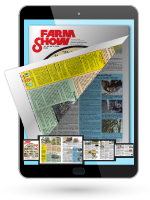
You must sign in, subscribe or renew to see the flip-book
New Slant On Milk, Manure Handling LIVESTOCK Buildings 4-4-27 Paul Longacre's new stall barn near Coopersburg, Lehigh County, Penn., looks conventional enough from the outside. But inside there's a startling difference - the floor is on a tilt. It slopes.
"By sloping the barn floor we've been able to utilize gravity flow for both milk and manure," Paul explains.
"As a result, we've cut costs and increased operating efficiency."
The sloping floor idea for the 60stall barn was designed by John Lapinski, Sellersville agricultural consultant, who says it incorporates some basic techniques used in Europe.
Manure flows by gravity through a deep gutter under the floor and out into a lagoon.
At the same time, sloping permits operation of a curb-level milk line instead of the customary overhead system. As an added bonus, a ventilation system that utilizes the under-thecurb gutters keeps odors to a minimum.
"Paul's son, Glen, and I built the forms, poured the concrete and worked out bugs as we went along," Lapinski says. The curb-level milk line was the work of Lapinski and Larry Eshelman of Longacre Electric Service, Surge dealer in Bally.
To provide gravity flow for the milk, the barn floor slopes gently - one inch to 10 feet - from each end toward the center, where four feeder lines meet two trunk lines going to the bulk tank.
"The low-level line means less vacuum is needed for milking," Eshelman explains.
"The milk doesn't have to be lifted to an overhead pipe. Instead it just flows downward by gravity. The reduced vacuum means less strain on the animals."
Because the milk line is in front of the cows a self-closing cover was designed to protect the stall cocks.
For manure handling, two specially-designed deep gutters are pitched toward one end of the barn, from where a 30-in. pipe leads to the lagoon. The gutters incorporate some unique features:
First, the gutters vary in depth from 30 in. at the high point to 6 ft. at the low point to provide the needed slope.
They are shaped somewhat like an inverted "V" being 22 in. wide at the top and 32 in. wide at the bottom.
Lapinski explains why: "We made the gutters smaller at the top primarily to save floor space. The wider bottom increases capacity and, at the same time, prevents manure from sticking to the sides."
Every 50 ft. the bottoms of the gutters are partially blocked by 8-in.
high dams, made of concrete block.
"The purpose of these dams," Lapinski says, "is to hold enough liquid to turn the manure into a slurry that will flow."
There's been no build-up of solids in more than four months of operation, he says.
"If this should happen, a few squirts of water from a hose will take care of it."
Even long hay that gets into the gutters accidentally poses no problem, he says.
Extra liquid to help make the slurry is provided by the twice daily cleaning of the grates over the gutters. A large push broom with hose attached is used. This chore takes only 15 min. twice a .day.
The grates are kept free of manure and about a gallon of water per cow goes into the gutters.
With a gravity flow manure system, adequate ventilation is a must, Lapinski says. The one he designed is simple and low cost, yet singularly effective.
A one-horsepower exhaust fan draws air in through adjustable louvers under the eaves of the barn, sucks it across the cows and down through the deep gutters. It is exhausted just above the slurry exit.
During winter, this single fan changes the air in the barn every 20 min., Lapinski says. He notes that in summer two additional fans will permit a change every two minutes. The writer noted very little odor in the barn during his visit.
Paul Longacre says the barn, made of block with insulated roof, and including the manure system, cost about $100,000. He says he figures he got his money's worth.
"The extra expense of the sloping floor and gutters was just about offset by what it would have cost to install and maintain mechanical cleaners. We don't have to worry about breakdowns or having to replace worn-out equipment in a few years.
"On top of that, we're saving on the c
To read the rest of this story, download this issue below or click here to register with your account number.