Self-Propelled Auger Makes Harvest Easier
 ✖  |
Grain farmer Dale Beamish used his spare time to simplify his busiest season. Beamish, who farms with his mom and brother at Jarvie, Alberta, found an easier way to fill his 65 bins at harvest time by building a self-propelled 13-in. dia. auger.
He built the auger itself totally from scratch and says it's built so strong he can even use it as a bin crane to pick up empty bins and move them.
He estimates the project took 250 hours to complete and his material cost was $4,800. The only things he purchased new were the main auger pipe, flighting, bearings, pulleys and belts; the rest was salvaged.
Beamish started with the engine and transmission from a Massey Harris 21 combine. The driveshaft is off the front of the engine that he uses for ground drive. The back of the engine is fitted with an independent automotive-type clutch and output shaft for driving the auger. The axle and chain-drive unit that powers the two drive wheels was widened out to 12 ft. for maximum stability.
The unit has four forward gears and one reverse, but since it's "geared low," it only travels about 6 mph maximum. It uses a hydraulic lever for steering the two smaller rear wheels.
Two steps lead to the open air operator platform which is located on the left side of the auger, facing the discharge end. A seat from a Massey Harris 21 combine was used.
The auger itself was made from scratch using a 60 ft. length of oilfield pipe.
The auger is top drive, using double 60 roller chain. The 90 degree gear box is from a White 8650 combine. The rear lift arms, which lift independently, are positioned on the center of the jackshaft and gearbox so that the belt tension doesn't change, no matter what height the auger is at.
A 13-ft. hydraulic cylinder under the auger tube is used to raise the discharge end and another smaller hydraulic cylinder under the rear lift arms is used to raise the intake end of the auger for transport or cleaning the hopper out.
About 5 ft. up from the auger base, two lights are mounted directly above the angle drive gear box. They provide good visibility when unloading at night into the integrated intake hopper.
Two steps from the hopper, is a control panel where the engine on/off switch, light switch, throttle and clutch for engaging or disengaging the auger are located. To simplify night moving, two additional lights are positioned about 15 ft. from the top of the auger.
There's no slip clutch or shear pin. Instead, when the bin is full, the auger plugs and stalls the Chrysler industrial engine. Then, Beamish simply moves the full auger to the next bin. The heavy driveline allows this to be done with no damage. Beamish says he's already plugged and stalled the auger more than 500 times.
Contact: FARM SHOW Followup, Dale Beamish, Beamish Seed Farms
, Box 67, Jarvie, Alberta, Canada, TOG 1HO (ph 780 954-2166 or 780 954-3960).
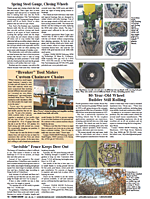
Click here to download page story appeared in.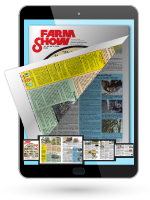
Click here to read entire issue
Self-Propelled Auger Makes Harvest Easier AUGERS Augers (29B) 23-6-6 Grain farmer Dale Beamish used his spare time to simplify his busiest season. Beamish, who farms with his mom and brother at Jarvie, Alberta, found an easier way to fill his 65 bins at harvest time by building a self-propelled 13-in. dia. auger.
He built the auger itself totally from scratch and says it's built so strong he can even use it as a bin crane to pick up empty bins and move them.
He estimates the project took 250 hours to complete and his material cost was $4,800. The only things he purchased new were the main auger pipe, flighting, bearings, pulleys and belts; the rest was salvaged.
Beamish started with the engine and transmission from a Massey Harris 21 combine. The driveshaft is off the front of the engine that he uses for ground drive. The back of the engine is fitted with an independent automotive-type clutch and output shaft for driving the auger. The axle and chain-drive unit that powers the two drive wheels was widened out to 12 ft. for maximum stability.
The unit has four forward gears and one reverse, but since it's "geared low," it only travels about 6 mph maximum. It uses a hydraulic lever for steering the two smaller rear wheels.
Two steps lead to the open air operator platform which is located on the left side of the auger, facing the discharge end. A seat from a Massey Harris 21 combine was used.
The auger itself was made from scratch using a 60 ft. length of oilfield pipe.
The auger is top drive, using double 60 roller chain. The 90 degree gear box is from a White 8650 combine. The rear lift arms, which lift independently, are positioned on the center of the jackshaft and gearbox so that the belt tension doesn't change, no matter what height the auger is at.
A 13-ft. hydraulic cylinder under the auger tube is used to raise the discharge end and another smaller hydraulic cylinder under the rear lift arms is used to raise the intake end of the auger for transport or cleaning the hopper out.
About 5 ft. up from the auger base, two lights are mounted directly above the angle drive gear box. They provide good visibility when unloading at night into the integrated intake hopper.
Two steps from the hopper, is a control panel where the engine on/off switch, light switch, throttle and clutch for engaging or disengaging the auger are located. To simplify night moving, two additional lights are positioned about 15 ft. from the top of the auger.
There's no slip clutch or shear pin. Instead, when the bin is full, the auger plugs and stalls the Chrysler industrial engine. Then, Beamish simply moves the full auger to the next bin. The heavy driveline allows this to be done with no damage. Beamish says he's already plugged and stalled the auger more than 500 times.
Contact: FARM SHOW Followup, Dale Beamish, Beamish Seed Farms
, Box 67, Jarvie, Alberta, Canada, TOG 1HO (ph 780 954-2166 or 780 954-3960).
To read the rest of this story, download this issue below or click
here to register with your account number.