1989 - Volume #13, Issue #2, Page #32
[ Sample Stories From This Issue | List of All Stories In This Issue | Print this story
| Read this issue]
He Built His Own Silo Unloader For $800
Two years ago Dave Linstad, Porterfield, Wis., built his own 12-ft. dia. silo unloader for $800, using "odds and ends" from around the farm, off-the-shelf parts and components from a junked Patz unloader.Linstad's first step was to build a bigger blower. He welded four 4-in. cupped paddles onto an impeller, removed from the old Patz unloader, increasing blower diameter to 24 in. A V-belt drives the blower at about 1,600 rpm. A 3-hp electric motor set on a sliding mount can be easily adjusted to maintain belt tension. Linstad built the blower housing from 3/16-in. steel plate, equipping it with a removeable side plate for easy access for maintenance.
In building the silage conveyor, Linstad welded cutter claws every 6 in. onto Patz triple 80 pitch cutter chain. The cutter chain is driven by a 1-in. jack shaft set in flangemountball bearings. The jack shaft powers a 60 pitch roller chain at a 4:1 reduction. An idler on a spring-loaded arm is used to change tension on the cutter chain's V-belt. As the cutter chain advances, a sprocket on the end of a Patz roller wheel chips off a 2-in. wide band of silage. At the same time, the frost chipper removes frozen silage. Linstad built it by welding eighteen 1/4-in. bars, 2-in. wide by 4-in. long, onto a 9-in. dia., 1/4-in. plate disc. The chipper bars are hard-faced for long wear.
The guide wheels - Patz 1-in. dia. hub wheels - can be adjusted to vary the amount of clearance between the frost chipper and the silo wall.
On the Patz unloader, the cutter chain was suspended between two drive wheels at a pre-set depth by a yoke. Linstad's model has only one drive wheel, salvaged from an old Starline unloader. It's advanced by a compound reduction drive, which is driven by a spur gear welded on the cutter chain drive shaft.
Linstad says his old silo unloader some-times cut unevenly due to uneven weight distribution. He solved the problem on his home-built unloader by fitting it with front-end weights from an Allis-Chalmers tractor. "This unloader cuts as even as a table top. There's no 'mound in the middle or bumps on the outside," notes Linstad.
He built the unloader tripod from 1/4-in. plate and 2-in. pipe, He used a worm-gear drive box, removed from a chopper box, to fabricate the winch and welded a steel plate with a hole in it to the outside of the blower housing to build a "lugging lift." "I use a 1/ 2 hp motor with a 16-in. V pulley on the winch input shaft to raise the unloader to the top of the silo in short order," says Linstad.
For more information, contact: FARM SHOW Followup, Dave Linstad, Rt. 1, Box 305, Porterfield, Wis. 54159 (ph 715 732-0793)
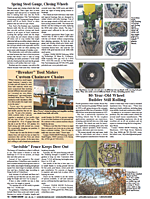
Click here to download page story appeared in.
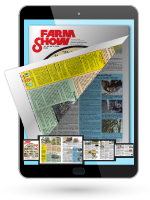
Click here to read entire issue
To read the rest of this story, download this issue below or click here to register with your account number.