1989 - Volume #13, Issue #2, Page #08
[ Sample Stories From This Issue | List of All Stories In This Issue | Print this story
| Read this issue]
He Improved Combine Performacne With Junk Parts
Bill Kreitzer, Elliott, Ill., used a little ingenuity and "junk parts" to make three inexpensive modifications that boost the productivity of his Deere 7700 combine.Kreitzer uses electric seat adjustment motors from junked-out cars to adjust the combine sieve and chaffer on-the-go; a $20 bicycle tachometer to monitor combine fan and header speed; and a safety switch from as riding lawn mower to monitor the grain level in the combine's tank.
Kreitzer first purchased two car seat motors from a local junkyard. He fastened the motors to the outside wall of the combine's cleaning chamber. He ran a length of hydraulic hose from the first motor to the chaffer adjustment lever and from the second motor to the sieve lever. Kreitzer notes that he uses hydraulic hose because it's stiff enough to act as a flexible adjustment shaft. The next step was to fasten two switches for the motors to the top of his Dickey-John grain loss monitor in the cab. He then removed the Dickey-John grain loss sensor from the straw walker and reinstalled it below the sieve, converting the grain loss monitor into a tailings return monitor.
"The straw walker monitor showed me how much grain was going over the straw walker but it couldn't help me control grain loss," says Kreitzer. "By repositioning the sensor below the sieve, I now know how much grain is going into the tailings return auger. If too much grain grain is being returned I can open up the sieve using the switch in the cab. I no longer have to get out of the cab and practically stand on my head to see how much grain is in the tailings return auger. This system is perfect for blending soy-bean varieties in different parts of the field to achieve an optimum average moisture content. Some varieties have higher moisture contents and bigger seed sizes than others. I now can adjust the sieve down and harvest soybeans in an-other part of the field without getting out of the cab to readjust the sieve. And if there's too much foreign material in the grain, I can open up the chaffer using the other switch in the cab."
Kreitzer estimates he spent about $100 to wire up the two servo motors.
A bicycle tachometer purchased for $20 from a local bicycle dealer lets Kreitzer monitor both fan and header speed. He added a two-way switch to the tachometer and mounted it in the cab. He then mounted a magnetic sensor on the fan blades and another one on a pulley on the feederhouse shaft that drives the combine's header. The tachometer measures the number of fan and feederhouse shaft revolutions. "By flipping the switch one way I can read fan speed and by flipping it the other way I can read header speed," notes Kreitzer.
His third invention is a grain tank shut-off. Kreitzer does at least 30% of his combining at night when it's difficult to see how much grain is in the tank. The problem was compounded when he added a 14-in. high extension which allows grain to completely cover the tank window. To solve the problem, he removed a 1/2-in. wide by 10-in. long safety switch from under the seat of a Deere 318 riding lawn mower (the switch is used to start and stop the mower when the driver gets on and off), bolted it to a 2-in. wide by 6-in. long plastic paddle, and mounted it near the top of the tank.
"Grain pushing against the plastic paddle turns on a light mounted on the cab's steering post column to alert me that the hopper is full. The light automatically shuts off when I unload the tank."
Contact: FARM SHOW Followup, Bill Kreitzer, P.O. Box 1, Elliott, Ill. 60933 (ph 217 784-4646).
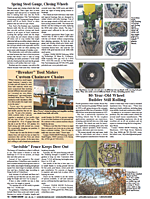
Click here to download page story appeared in.
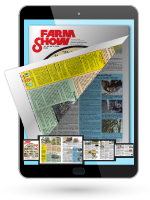
Click here to read entire issue
To read the rest of this story, download this issue below or click here to register with your account number.