Swather Built From Old Combine
"My home-built 56-ft. wide self-propelled swather does the job of two 28-ft. wide pull-type swathers and cost only $18,000 to build," says Roger Allemand, Dollard, Sask., about the swather he built from a junked-out 1969 Deere 730 combine and two old Massey Ferguson model 35 pull-type swathers.
Allemand paid $2,500 for the combine and $5,300 for the swathers. He stripped away everything on the combine except for the cab, chassis, and drive train. He mounted cutting tables and reels from the swathers side by side on a home-built steel frame that's bolted to the front of the combine. He moved the 150 hp 6-cylinder 303 cu. in. engine to the rear of the combine to counter-balance the weight of the swathers, which fold back on either side of the combine to a 30-ft. transport width.
"We had been using two 1978 28-ft. wide pull-type swathers which required two men to operate," says Allemand, who uses the swather to harvest wheat, barley, and durum. "I wanted a self-propelled swather, but I didn't want to spend up to $75,000 for a commercial machine this size. It has saved me both money and manpower."
Allemand shortened the combine wheel-base 3 ft. to allow for sharper turns. He replaced the combine's original tires with larger 20.8 by 38's on front and 9.00 by 24's at the rear. The taller tires provide 8 in. more clearance to keep the combine from disturbing the swath after it's laid down. He used 4-in. sq. steel tubing to build a 12-ft. wide, 3-ft. high support frame at the front of the combine. He attached another frame to each swather. The two swather frames are hinged onto the center mounting frame by two steel pins at each end of the frame. One pair of hydraulic cylinders lifts the combine-mounted frame to keep the entire swather level in the field. A second pair of cylinders individually controls each swather table keeping them at the proper cutting height. A third pair of cylinders tucks the swathers against the sides of the combine for transport.
The swather is equipped with six hydraulic motors - two for the knives, two for the table, and two for the reel. Allemand removed the flywheel-type pitman drives that powered the cutting bars on the original swathers and replaced them with wobble box drives.
Allemand welded a plate to each end of a length of 16-in. dia. pipe to build a 45-gal. hydraulic reservoir. A two-stage hydraulic pump is driven directly off the engine crank-shaft and controls all hydraulic operations. Each stage delivers 24 gpm for a total of 48 gpm.
Contact: FARM SHOW Followup, Roger Allemand, P.O. Box 27, Dollard, Saskatchewan, Canada S0N 0S0 (ph 306 297-3259).
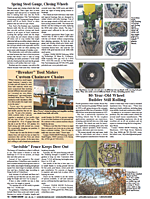
Click here to download page story appeared in.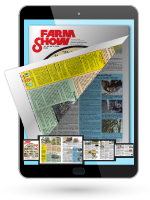
Click here to read entire issue
Swather built from old combine COMBINES Conversions 14-2-16 "My home-built 56-ft. wide self-propelled swather does the job of two 28-ft. wide pull-type swathers and cost only $18,000 to build," says Roger Allemand, Dollard, Sask., about the swather he built from a junked-out 1969 Deere 730 combine and two old Massey Ferguson model 35 pull-type swathers.
Allemand paid $2,500 for the combine and $5,300 for the swathers. He stripped away everything on the combine except for the cab, chassis, and drive train. He mounted cutting tables and reels from the swathers side by side on a home-built steel frame that's bolted to the front of the combine. He moved the 150 hp 6-cylinder 303 cu. in. engine to the rear of the combine to counter-balance the weight of the swathers, which fold back on either side of the combine to a 30-ft. transport width.
"We had been using two 1978 28-ft. wide pull-type swathers which required two men to operate," says Allemand, who uses the swather to harvest wheat, barley, and durum. "I wanted a self-propelled swather, but I didn't want to spend up to $75,000 for a commercial machine this size. It has saved me both money and manpower."
Allemand shortened the combine wheel-base 3 ft. to allow for sharper turns. He replaced the combine's original tires with larger 20.8 by 38's on front and 9.00 by 24's at the rear. The taller tires provide 8 in. more clearance to keep the combine from disturbing the swath after it's laid down. He used 4-in. sq. steel tubing to build a 12-ft. wide, 3-ft. high support frame at the front of the combine. He attached another frame to each swather. The two swather frames are hinged onto the center mounting frame by two steel pins at each end of the frame. One pair of hydraulic cylinders lifts the combine-mounted frame to keep the entire swather level in the field. A second pair of cylinders individually controls each swather table keeping them at the proper cutting height. A third pair of cylinders tucks the swathers against the sides of the combine for transport.
The swather is equipped with six hydraulic motors - two for the knives, two for the table, and two for the reel. Allemand removed the flywheel-type pitman drives that powered the cutting bars on the original swathers and replaced them with wobble box drives.
Allemand welded a plate to each end of a length of 16-in. dia. pipe to build a 45-gal. hydraulic reservoir. A two-stage hydraulic pump is driven directly off the engine crank-shaft and controls all hydraulic operations. Each stage delivers 24 gpm for a total of 48 gpm.
Contact: FARM SHOW Followup, Roger Allemand, P.O. Box 27, Dollard, Saskatchewan, Canada S0N 0S0 (ph 306 297-3259).
To read the rest of this story, download this issue below or click
here to register with your account number.