You have reached your limit of 3 free stories. A story preview is shown instead.
To view more stories
(If your subscription is current,
click here to Login or Register.)
Dryer Heat Exchanger
An Ohio farmer cut his per bushel drying costs with a wrap around heat exchanger he built onto his Farm Fans AB 12 grain dryer.
Ken Studer, who farms near Tim, says the exchanger worked without a hitch in 1986. "I've owned the dryer since 1984. That first year, drying costs were 15 cents per bu., drying down from
..........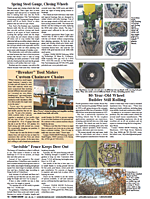
You must sign in, subscribe or renew to see the page.
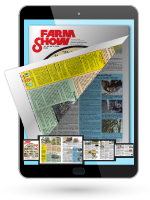
You must sign in, subscribe or renew to see the flip-book
Dryer Heat Exchanger GRAIN DRYERS Grain Dryers (29E) 11-4-8 An Ohio farmer cut his per bushel drying costs with a wrap around heat exchanger he built onto his Farm Fans AB 12 grain dryer.
Ken Studer, who farms near Tim, says the exchanger worked without a hitch in 1986. "I've owned the dryer since 1984. That first year, drying costs were 15 cents per bu., drying down from 25% moisture to 15.5%. LP at that time cost 59.9 cents per gal. Last fall, when I dried corn from 20% to 14.5% at an LP cost of 45.9 cents per gal., per bu. drying costs were 5.2 cents. Under most conditions, I feel I can can reduce total drying costs at least 3 cents per bushel," he says.
The heat exchanger consists of 96 pipes running horizontally the length of the dryer, 48 on each side. The pipes are shrouded by a sheet metal housing. Fresh air is sucked in through the pipes, which protrude from the end opposite the dryer's 36-in. fan, while hot, moist exhaust air from the dryer flows up around the outside of the fresh air pipes. Atop the horizontal pipes, a series of short, vertically-mounted pipes act as a secondary heat exchange chamber. Moist, hot air exits upward through the pipes and fresh air is pulled in around them. This top chamber was built before the lower part of the exchanger. Studer changed the design for the lower chamber, which he says works best.
A sheet metal housing encloses the entire fan and burner assembly. A full-size door allows easy access for maintenance.
Contact: FARM SHOW Followup, Ken Studer, 7633 Auburn Center Rd., Tiro, Ohio 44887 (ph 419 347-6718).
To read the rest of this story, download this issue below or click
here to register with your account number.