You have reached your limit of 3 free stories. A story preview is shown instead.
To view more stories
(If your subscription is current,
click here to Login or Register.)
Mulcher-Packer Made With Harrows
"In our area, most farmers plant a winter pasture comprised of rye grass, oats, wheat, legumes, or a combination of these. Tillage is kept to a minimum so a lot of residue is left on the surface," says Kevin Stilley, Loranger, Louisiana.
"The field is prepared with an offset disk and a pass with a pulverizing di
..........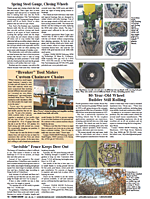
You must sign in, subscribe or renew to see the page.
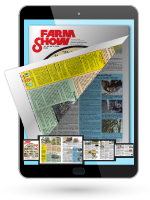
You must sign in, subscribe or renew to see the flip-book
Mulcher-Packer made with Harrows TILLAGE EUIPMENT Harrows 17-3-11 "In our area, most farmers plant a winter pasture comprised of rye grass, oats, wheat, legumes, or a combination of these. Tillage is kept to a minimum so a lot of residue is left on the surface," says Kevin Stilley, Loranger, Louisiana.
"The field is prepared with an offset disk and a pass with a pulverizing disk along with a spike-toothed harrow. Seed and fertilizer is then broadcast by a custom applicator and we work it in with a mulcher-packer. We recently built our own mulcher-packer because our old unit was worn out and also, we didn't like the design of conventional units which are fitted with spring tines that cause residue to ball up and clog the machine. My home-built unit uses harrow sections fitted with stiff, straight teeth that don't plug up and leave the field smooth with most of the residue on top of the ground to hold soil in place. After one year of use, we think it works great.
"We used packer rollers from an old Brillion LTF-96 Surestand Seeder. It cost about $200 to rebuild the rollers, including bolts, bearings, grease fittings, and packer wheels. We made the main frame of the unit out of 4-in. channel iron, 3 by 3-in. angle iron, and 3/8-in. thick steel plate for corner braces. A local welding company put it together for us for $500. We bought the harrow sections from a local equipment company for $550. They're connected to the front crossbar by short lengths of chain. The entire unit is 9 ft. wide and 16 ft. long."
Contact: FARM SHOW Followup, Kevin Stilley, Stilley Dairy Farm, Rt. 1, Box A-142, Loranger, La. 70446-9801.
To read the rest of this story, download this issue below or click
here to register with your account number.