You have reached your limit of 3 free stories. A story preview is shown instead.
To view more stories
(If your subscription is current,
click here to Login or Register.)
Farm-Built Manure Handling Equipment
Using all junked parts, including a salvaged stainless steel milk truck tank, Ian MacCuaig, Dalhousie Station, Que., built a manure handling system that he says, rivals the most expensive equipment on the market.
In addition to high-capacity pump and spreader wagon, MacCuaig built a manure transfer system that mo
..........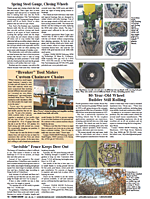
You must sign in, subscribe or renew to see the page.
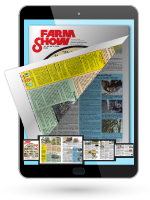
You must sign in, subscribe or renew to see the flip-book
Farm-Built Manure Handling Equipment MANURE HANDLING Equipment 10-4-11 Using all junked parts, including a salvaged stainless steel milk truck tank, Ian MacCuaig, Dalhousie Station, Que., built a manure handling system that he says, rivals the most expensive equipment on the market.
In addition to high-capacity pump and spreader wagon, MacCuaig built a manure transfer system that moves manure from the barn to his lagoon ù winter and summer ù with no machinery whatsoever.
MacCuaig's first project was his high-capacity manure pump that'll fill a 2,000 gal. tank in 3 min. He started with a construction pump he found in a scrap yard and mounted it on a portable frame. At first he powered it with a salvaged truck engine but the engine turned too fast so he switched to a tractor pto. Because the pto turned the opposite direction, he searched the salvage yards for a gear-box that reverses the drive and also boosts tractor pto speed from 540 to 1100. He had to machine a coupler to fit the gearbox. A chain drive powers the pump. It's all mounted on a portable frame built from the chassis of a wrecked Toyota car.
The intake pipe on the pump is 4 in. in dia and the outtake 5 in. The pump could handle up to a 6 in. dia. pipe but MacCuaig says the bigger pipe would be too hard to handle.
"I've used it for 2 years without a hitch. Does the work of an $8,000 rig," states MacCuaig.
His next project was to build a spreader truck from a salvaged stainless steel milk truck tank. He bought it for $1,000 and mounted it on a dump truck chassis purchased for $100. He cut away the front cab and engine of the truck and built a cradle to precisely support the shape of the milk tank. To save weight, he cut away the outer shell and cork insulation of the double-lined milk truck tank before mounting it on the truck.
Manure is pulled out of the truck and spread by a 4-bladed, pto-powered impellor fan that literally blows the manure up and out the back of the tank where it hits a deflector plate that spreads it out over a 30 to 35-ft. area.
"All parts that come into contact with the manure are made from stainless steel so there's very little wear or deterioration," says MacCuaig, noting that he built the fan-type impellor, which is belt-driven off the pto, from scratch. He says the entire 2,000 gal. tank can be emptied in about 5 min. "The hardest part was building the cradle. It must provide a lot of support to the tank because of the tremendous weight."
Perhaps the most important part of MacCuaig's manure handling system is the way he gets manure from his dairy barn to his 80-ft. dia. (10-ft. deep) lagoon. He simply built a huge concrete culvert that's 10 ft. deep, 6 ft. across and 50 ft. long. The barn cleaner dumps manure into the culvert and MacCuaig adds water. The culvert is built level and manure finds it's own level, gradually working its way out to the lagoon, which is located at the far end of the concrete culvert.
"I didn't want to slope the culvert because that causes solids to separate out. This way it all works its way to the lagoon without any piston pumps, air pressure or other machinery. During winter, it works it's way out and pushes in under frozen buildup on the pond. It's completely trouble-free," says MacCuaig, noting that he spent about $7,000 to build the manure culvert and dig the lagoon.
Contact: FARM SHOW Followup, Ian MacCuaig, Dalhousie Station, Que. J0P 1G0 Canada (ph 514 764-3464).
To read the rest of this story, download this issue below or click
here to register with your account number.