You have reached your limit of 3 free stories. A story preview is shown instead.
To view more stories
To view more stories
SUBSCRIBE OR RENEW NOW
(If your subscription is current, click here to Login or Register.)1994 - Volume #18, Issue #5, Page #17
[ Sample Stories From This Issue | List of All Stories In This Issue]
High Speed Tractor Built For Custom Bailing
"It saves time and rides much smoother than a conventional tractor. It's also fitted with controls that make my round baler a lot easier to operate," says custom hay baler Dan Krueger, of Shawano, Wis., about the "high-speed" tractor he built using parts from an old pickup and combine. It lets him pull his Deere 435 ro..........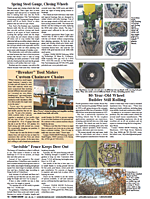
You must sign in, subscribe or renew to see the page.
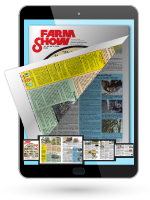
You must sign in, subscribe or renew to see the flip-book
High Speed Tractor Built For Custom Bailing BALERS Balers It saves time and rides much smoother than a conventional tractor It s also fitted with controls that make my round baler a lot easier to operate says custom hay baler Dan Krueger of Shawano Wis about the high-speed tractor he built using parts from an old pickup and combine It lets him pull his Deere 435 round baler at speeds up to 11 mph in the field and up to 50 mph on the highway
The speedy tractor was built on the frame of a 1970 Chevrolet 3/4-ton pickup and has dual 20-in lugged truck tires on the rear axle with single 20-in truck tires in front Air bags off a semi truck mount under the rear axle The cab and hydrostatic transmission came out of a Deere 7700 combine The hydrostatic transmission is connected to a 4-speed transmission out of a junked truck Power is supplied by a Deere 4-cyl turbocharged industrial diesel engine with 109 hp All baler operations are controlled by a single joystick lever in the cab that s equipped with four electric switches
Krueger also mounted tandem axles on the baler
People can t believe it when they see it says Krueger who used the tractor for the first time last summer I built it because I bale hay over a 40-mile area and spend a lot of time on the highway between jobs I wanted more speed on the road and a better ride in the field My baler can handle a lot of hay but in rough fields with a conventional tractor I couldn t go fast because I could hardly stay in the seat The combination of the air bags suspension seat dual rear truck tires and tandem axles on the baler smoothes out the ride The lugged truck tires provide traction and flotation
The 4-speed transmission has a lot of range and power in first gear which works great for baling I can crawl along or go up to 11 mph in first gear I can go up to 50 mph in third gear on the highway which is about as fast as I dare go pulling a 2-ton baler I modified the pickup s brake system to double the brakes stopping power and mounted a rollbar designed for a Deere tractor behind the cab so that if I m ever forced into a ditch at high speed I ll have roll-over protection I also use a seat belt
The tractor has 17 in of clearance even under the hitch so it can handle big windrows I can control the amount of pressure in each airbag and make the tractor lean to either side for use on hillsides
I simply push a hydrostatic lever ahead to go forward and pull it back to go in re-verse I can control all baler operations with my thumb by using four 2-way switches mounted on the lever
I bought the cab used for $500 and paid $5 000 for a new engine My total cost was about $12 000 which is less than half the cost of a comparable new tractor I didn t modify the baler at all so if there s ever a problem with the tractor I can unhook it and use a conventional tractor
Krueger bought the junked pickup frame for $50 and cut it off just behind the rear axle then removed the rear coil springs and replaced them with air bags The combine s hydrostatic transmission ran in the opposite direction as the engine so he mounted the engine backward The hydrostatic transmission is connected to a 4-speed truck transmission from an old 1-ton IH truck The 4-speed transmission runs backward in order to match up with the hydrostatic transmission
Krueger tipped the differential upside down on the back axle so the tractor wheels would go in the right direction
A 3-groove pulley bolted onto the engine crankshaft belt drives a shaft that runs along the left side of the pickup frame back to a reduction gearbox The gearbox chain drives the pto shaft and reduces shaft speed from 1 250 rpm s to 600 rpm s The pto runs a little faster than the normal 540 rpm s allowing me to throttle the engine down and conserve fuel says Krueger An air cylinder mounted next to the engine is used to control a spring loaded idler that engages or disengages the belts
All hydraulic controls are powered by a 2-way air cylinder mounted at the back of the tractor The air cylinder is powered by an old air conditioner pump that Krueger converted into an air compressor An electric clutch connecled to a pressure switch kicks the compressor on or off An eleclric power window conlrol activates solenoids that operate the air controls
The compressor and air controls are mounted in n box outside the cab Krueger activivates the controls by using the four switches on the hydrostatic lever One switch opens or closes the baler endgate one starts or stops the pto one electronically controls the engine throttle and one automatically turns the pro off as soon us the endgate is opened and turns it on as soon as the endgate is closed The engine throutle control is powered by an electric window motor salvaged from an old car that s bolted to the side of the engine
Krueger used steel plate to close up the back of the combine cab where the grain tank had been and also the right side of the cab where the engine was mounted He mounted a window in the back side of the cab and put a mirror in front of it inside the cab By looking at the mirror I can see the bale as it starts rolling without always having to look behind notes Krueger
The cab has three front-operated brake pedals – individual pedals for the rear wheels and a combination pedal for the front wheels The steering wheel and column came out of an old Chevrolet Citation car Electronic controls in the column are used to operate the dimmer switch windshield wiper and directional lights Krueger made the fenders by bolting lengths of 12-in wide rubber belting to a length of curved steel The belting is flexible so if it hits something it ll bend without breaking he notes
He welded a tractor drawbar to a hitch he made from 3 by 6-in angle iron and welded it to the back of the pickup frame He designed a pattern for the hood and had it made by a local fire truck manufacturer The 4-in dill muffler was borrowed from a semi truck A 35-ga1 fuel tank mounts behind the cab
The pickup s 17 1/2-in wheel rims were welded into the truck tires 20-in rims He used square tubing off an old plow and a 2-in dia Square tubing off an old plow and a 2-in dia Steel shaft to make the tandem axle for the baler
Contact: FARM SI·IOW Followup Dan Krueger Rr 2 Box 33 Shawano Wis 54166 ph 715 526-3995
The speedy tractor was built on the frame of a 1970 Chevrolet 3/4-ton pickup and has dual 20-in lugged truck tires on the rear axle with single 20-in truck tires in front Air bags off a semi truck mount under the rear axle The cab and hydrostatic transmission came out of a Deere 7700 combine The hydrostatic transmission is connected to a 4-speed transmission out of a junked truck Power is supplied by a Deere 4-cyl turbocharged industrial diesel engine with 109 hp All baler operations are controlled by a single joystick lever in the cab that s equipped with four electric switches
Krueger also mounted tandem axles on the baler
People can t believe it when they see it says Krueger who used the tractor for the first time last summer I built it because I bale hay over a 40-mile area and spend a lot of time on the highway between jobs I wanted more speed on the road and a better ride in the field My baler can handle a lot of hay but in rough fields with a conventional tractor I couldn t go fast because I could hardly stay in the seat The combination of the air bags suspension seat dual rear truck tires and tandem axles on the baler smoothes out the ride The lugged truck tires provide traction and flotation
The 4-speed transmission has a lot of range and power in first gear which works great for baling I can crawl along or go up to 11 mph in first gear I can go up to 50 mph in third gear on the highway which is about as fast as I dare go pulling a 2-ton baler I modified the pickup s brake system to double the brakes stopping power and mounted a rollbar designed for a Deere tractor behind the cab so that if I m ever forced into a ditch at high speed I ll have roll-over protection I also use a seat belt
The tractor has 17 in of clearance even under the hitch so it can handle big windrows I can control the amount of pressure in each airbag and make the tractor lean to either side for use on hillsides
I simply push a hydrostatic lever ahead to go forward and pull it back to go in re-verse I can control all baler operations with my thumb by using four 2-way switches mounted on the lever
I bought the cab used for $500 and paid $5 000 for a new engine My total cost was about $12 000 which is less than half the cost of a comparable new tractor I didn t modify the baler at all so if there s ever a problem with the tractor I can unhook it and use a conventional tractor
Krueger bought the junked pickup frame for $50 and cut it off just behind the rear axle then removed the rear coil springs and replaced them with air bags The combine s hydrostatic transmission ran in the opposite direction as the engine so he mounted the engine backward The hydrostatic transmission is connected to a 4-speed truck transmission from an old 1-ton IH truck The 4-speed transmission runs backward in order to match up with the hydrostatic transmission
Krueger tipped the differential upside down on the back axle so the tractor wheels would go in the right direction
A 3-groove pulley bolted onto the engine crankshaft belt drives a shaft that runs along the left side of the pickup frame back to a reduction gearbox The gearbox chain drives the pto shaft and reduces shaft speed from 1 250 rpm s to 600 rpm s The pto runs a little faster than the normal 540 rpm s allowing me to throttle the engine down and conserve fuel says Krueger An air cylinder mounted next to the engine is used to control a spring loaded idler that engages or disengages the belts
All hydraulic controls are powered by a 2-way air cylinder mounted at the back of the tractor The air cylinder is powered by an old air conditioner pump that Krueger converted into an air compressor An electric clutch connecled to a pressure switch kicks the compressor on or off An eleclric power window conlrol activates solenoids that operate the air controls
The compressor and air controls are mounted in n box outside the cab Krueger activivates the controls by using the four switches on the hydrostatic lever One switch opens or closes the baler endgate one starts or stops the pto one electronically controls the engine throttle and one automatically turns the pro off as soon us the endgate is opened and turns it on as soon as the endgate is closed The engine throutle control is powered by an electric window motor salvaged from an old car that s bolted to the side of the engine
Krueger used steel plate to close up the back of the combine cab where the grain tank had been and also the right side of the cab where the engine was mounted He mounted a window in the back side of the cab and put a mirror in front of it inside the cab By looking at the mirror I can see the bale as it starts rolling without always having to look behind notes Krueger
The cab has three front-operated brake pedals – individual pedals for the rear wheels and a combination pedal for the front wheels The steering wheel and column came out of an old Chevrolet Citation car Electronic controls in the column are used to operate the dimmer switch windshield wiper and directional lights Krueger made the fenders by bolting lengths of 12-in wide rubber belting to a length of curved steel The belting is flexible so if it hits something it ll bend without breaking he notes
He welded a tractor drawbar to a hitch he made from 3 by 6-in angle iron and welded it to the back of the pickup frame He designed a pattern for the hood and had it made by a local fire truck manufacturer The 4-in dill muffler was borrowed from a semi truck A 35-ga1 fuel tank mounts behind the cab
The pickup s 17 1/2-in wheel rims were welded into the truck tires 20-in rims He used square tubing off an old plow and a 2-in dia Square tubing off an old plow and a 2-in dia Steel shaft to make the tandem axle for the baler
Contact: FARM SI·IOW Followup Dan Krueger Rr 2 Box 33 Shawano Wis 54166 ph 715 526-3995
To read the rest of this story, download this issue below or click here to register with your account number.