Cadillac Machine Shed Built From Junked Steel
"A lot of people said it couldn't be done," says David Heinze, Belgrade, Minn., about the open-front, high-clearance "Cadillac" machine shed he built from 10 and 12-in. steel I-beams and 12-in. wide channel iron salvaged from four old township highway bridges.
The 72-ft. wide, 34-ft. deep shed is sup-ported in front by just four 5 by 10-in. I-beams spaced 24 ft. apart.
"I built it because I needed a bigger ma-chine shed. The door openings on my old shed were so narrow that I had to drive my 6-row combine within inches of the door-way posts in order to fit the combine into the shed. The 24 ft. openings between posts on my new shed leave plenty of room for my
combine, and the 14 It. 1 in. of vertical clearance lets me drive in without having to fold down the combine's extension hop-per," says Heinze.
"I paid $400 for the scrap bridge steel and another $1,600 for some new I-beam rafters. The entire building cost about $6,000 to build."
Heinze designed and built the entire shed without using a blueprint or any professional help. Many of the I-beams he used were 30 ft. long and weighed up to 1,200 lbs. each. Some were bent and twisted. He straightened them with his own home-built hydraulic press designed specially to straighten out the big beams (the press itself is built from some of the salvaged bridge beams). After straightening out the beams, Heinze laid them on his 30-ft. long welding table and cut and spliced them together to the proper length. Each of the walls was constructed on the ground and then lifted into place by a rented hydraulic construction crane. Rafters were then individually lifted into place and welded to the walls. The entire framework was set up and welded together in one day with the help of 11 men and two portable welders.
"It was a real challenge," says Heinze. "It took 10 days to cut, straighten, and weld all of the I-beams together to the proper lengths. Most of the beams are built from high-tensile steel and are very strong. I fish-plated any steel that was stressed or rusted out. Once the framework was in place it took five more days to install the roof and sides. All of the beams were pre-drilled so that 2 by 4's supporting the tin roof could be bolted to them."
For more information, contact: FARM SHOW Followup, David Heinze, 41008 275th St., Belgrade, Minn. 56312 (ph 612 254-8438).
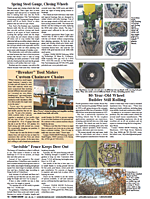
Click here to download page story appeared in.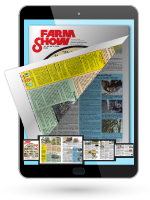
Click here to read entire issue
Cadillac machine shed built from junked steel BUILDINGS Miscellaneous 15-3-24 "A lot of people said it couldn't be done," says David Heinze, Belgrade, Minn., about the open-front, high-clearance "Cadillac" machine shed he built from 10 and 12-in. steel I-beams and 12-in. wide channel iron salvaged from four old township highway bridges.
The 72-ft. wide, 34-ft. deep shed is sup-ported in front by just four 5 by 10-in. I-beams spaced 24 ft. apart.
"I built it because I needed a bigger ma-chine shed. The door openings on my old shed were so narrow that I had to drive my 6-row combine within inches of the door-way posts in order to fit the combine into the shed. The 24 ft. openings between posts on my new shed leave plenty of room for my
combine, and the 14 It. 1 in. of vertical clearance lets me drive in without having to fold down the combine's extension hop-per," says Heinze.
"I paid $400 for the scrap bridge steel and another $1,600 for some new I-beam rafters. The entire building cost about $6,000 to build."
Heinze designed and built the entire shed without using a blueprint or any professional help. Many of the I-beams he used were 30 ft. long and weighed up to 1,200 lbs. each. Some were bent and twisted. He straightened them with his own home-built hydraulic press designed specially to straighten out the big beams (the press itself is built from some of the salvaged bridge beams). After straightening out the beams, Heinze laid them on his 30-ft. long welding table and cut and spliced them together to the proper length. Each of the walls was constructed on the ground and then lifted into place by a rented hydraulic construction crane. Rafters were then individually lifted into place and welded to the walls. The entire framework was set up and welded together in one day with the help of 11 men and two portable welders.
"It was a real challenge," says Heinze. "It took 10 days to cut, straighten, and weld all of the I-beams together to the proper lengths. Most of the beams are built from high-tensile steel and are very strong. I fish-plated any steel that was stressed or rusted out. Once the framework was in place it took five more days to install the roof and sides. All of the beams were pre-drilled so that 2 by 4's supporting the tin roof could be bolted to them."
For more information, contact: FARM SHOW Followup, David Heinze, 41008 275th St., Belgrade, Minn. 56312 (ph 612 254-8438).
To read the rest of this story, download this issue below or click
here to register with your account number.