You have reached your limit of 3 free stories. A story preview is shown instead.
To view more stories
(If your subscription is current,
click here to Login or Register.)
Air Seeder Better Than Anything On Market
Using the best parts from both commercially-built press drills and a brand new air seeder, Brockton, Montana farmer Wayne Deubner designed what he thinks is a.world class planting machine that gives him the best features of both drills and air seeders without any of the drawbacks.
Last winter Deubner took his ide
..........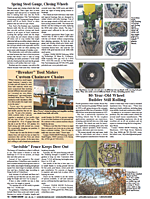
You must sign in, subscribe or renew to see the page.
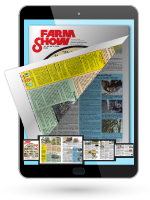
You must sign in, subscribe or renew to see the flip-book
Air Seeder Better Than Anything On Market PLANTING EQUIPMENT Air Seeders 17-4-25 Using the best parts from both commercially-built press drills and a brand new air seeder, Brockton, Montana farmer Wayne Deubner designed what he thinks is a.world class planting machine that gives him the best features of both drills and air seeders without any of the drawbacks.
Last winter Deubner took his ideas to Harlow Strandlund at Strandlund Welding & Machine Works in Homestead, Mont., who helped put the machine together in his shop.
Deubner's ideas for the machine grew out of his experiences with both types of seeders. Several years ago he switched from drills to an early Prasco air seeder mounted on a heavy-duty field cultivator. Not satisfied with the results, he switched back to conventional press drills. The problem with the drills was the difficulty in moving ganged drills from field to field and the limited seed capacity.
Once he got the idea of combining the best features of both machines, Deubner bought four used Deere double disc drills and a brand new Deere 787 air seeder which came complete with stands, electronics, and so on. At that point, he started consulting with Strandlund Welding & Machine Works.
The drill they built consists of three main components - the up-front field cultivator, a built-from-scratch center section that consists of double disk openers and packer wheels, and the trailing air seeder tank. The drill is 42 ft. wide with 7-in. row spacing, meaning there are 72 runs in all.
The frame for the center planting section is made out of heavy 4 by 8-in. tubing with 1/2-in. thick sidewalls. The heavy frame-work provides the needed strength and also the weight necessary to provide the packing action. Disk openers mount across the front, mounted on angle iron framework from the parent drills. Packer wheels mount in a row behind. Each of the solid packer wheels was recapped with angled rings and the centers were replaced with self-aligning ball-bearings to fit 1 1/2-in. shafting. An oscillating framework was made for each section of eight wheels. They, in turn, mount to the main framework which is in three sections. Wings are folded by two 5 by 36-in. lift cylinders. Front depth control dolly wheels were taken from IH grain drill carriers. Rear wheels are for transport only and are each fitted with an oscillating axle and a hydraulic cylinder.
"It's easy to use. When you pull out of the field, you wing up the cultivator and drill unit with a single lever since they're plumbed into the same hydraulic circuit. Transport wheels lift the entire drill to about 6 in. of clearance and the cultivator and drill are the same width and height," says Strandlund. "Other than connecting plumbing and the heavy-duty hitch, the cultivator is not altered and can simply be unhooked to use alone.
"Any type of air seeder could be used and it could be pulled between the cultivator and drill or pulled directly behind the tractor with everything else pulled behind it. Hitches are designed so the tractor, cultivator, drill and seed tank can be turned in a radius no larger than if you were pulling a gang of drills the same width.
"Every part of this combo drill is proven. The components are just put together a different way. Packer wheels provide a firm packing action, which is missing from most air drills, and because there were beefed up they will work for many years without wearing out. One big benefit is that the entire seeder is built low, compact and neat yet all components am easy to see and service.
"We could build a similar unit, minus the cultivator, for about $45,000. it could-be more or less depending on what percentage of new or used parts we used."
Contact FARM SHOW Followup, Harlow Strandlund, Strandlund Welding & Machine Works, 552 County Line, Home-stead, Mont. 59242 (ph 406 963-2574).
To read the rest of this story, download this issue below or click
here to register with your account number.