1994 - Volume #18, Issue #3, Page #38
[ Sample Stories From This Issue | List of All Stories In This Issue | Print this story
| Read this issue]
Bale Dryer Saves Wet Hay
The summer of 1993 was one of the wettest on record in Wisconsin history but Dan Kamps, a commercial hay-grower near Belmont, saved nearly all of his crop thanks to a forced-air bale dryer he built a year ago.He now bales hay at up to 35 percent moisture without worrying about losing quality in storage.
He built a lean-to alongside the 20-ft. sidewall of his hay shed to house the dryer, which is 66-ft. long and 8 ft. wide and can handle 540 bales per batch. The drying floor is made of concrete slats spaced 2 in. apart (he got the slats from a relative who was modifying a beef barn) resting on concrete ledges over a 4-ft. deep hot air tunnel. He put a layer of heavy steel mesh over the slats to add enough strength so the floor would support a tractor and loader weighing up to 9,000 lbs.
A 28-in. dia. 10-hp. grain bin dryer blows 100? to 110? heated air into the tunnel and up through the piles of bales on the slats. Layers of bales are offset about 3 in. to keep hot air from escaping and he draped canvas over the sides of the bale stacks to keep hot air from getting out. This year, he plans to add mechanically controlled wood side-walls that close in around the bales.
It takes 1 to 11/2 hrs. to load or unload the dryer, which is controlled by thermostats at either end of the drying floor. Drying bales down to a safe moisture level takes 1 to 1 1/ 2 days. Hay generally dries uniformly from one end of the dryer to the other but not from the bottom to the top of the stacks. He usually runs the dryer until bottom-layer bales test 16 to 17% moisture, the middle layer about 20%, and the top layer about 22%. Hay in the top layer could spoil at that moisture level so only bales treated with a low rate of proprionic acid are placed in the top layer.
Kamps estimates summer-long fuel and electricity costs averaged about $20 per ton of hay dried but he plans to reduce that by a third by increasing efficiency of the system. For instance, he's installing a larger 42-in. fan with a 15 hp. motor to increase air flow.
He spent $5,000 on the building and $6,000 on the concrete floor. However, he sold the dried hay for up to $170 a ton, much of which might otherwise have gone to waste in the field.
Contact: FARM SHOW Followup, Dan Kamps, Belmont, Wis. 53510. (Neil Tietz in Hay & Forage Grower)
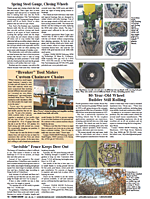
Click here to download page story appeared in.
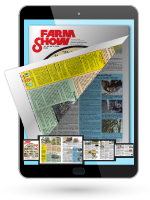
Click here to read entire issue
To read the rest of this story, download this issue below or click here to register with your account number.