You have reached your limit of 3 free stories. A story preview is shown instead.
To view more stories
(If your subscription is current,
click here to Login or Register.)
Build Yourself A Silo House
About 100 families in the Eastern U.S. are enjoying the comforts, convenience and, most important, the cost-saving features of silo houses.
"Cost for the outer shell and roof runs somewhere between $3,400 and $6,500, depending on size," Al Gurney, sales engineer, told FARM SHOW. "When a new silo house goes up in
..........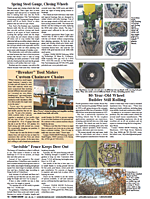
You must sign in, subscribe or renew to see the page.
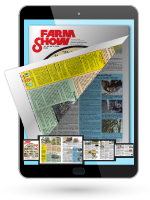
You must sign in, subscribe or renew to see the flip-book
Build Yourself A Silo House CROP STORAGE Silos (50) 1-4-7 About 100 families in the Eastern U.S. are enjoying the comforts, convenience and, most important, the cost-saving features of silo houses.
"Cost for the outer shell and roof runs somewhere between $3,400 and $6,500, depending on size," Al Gurney, sales engineer, told FARM SHOW. "When a new silo house goes up in an area, pretty soon there are three or four more. Soaring costs for conventional housing and the energy crisis have triggered a lot of interest," says Gurney who has been planner and "godfather" to most of the 100 or so silo houses Unadilla Silo has sold to date. They've gone to 15 different states, including Minnesota, Georgia and California. "One buyer from Northern California came out with a rental trailer to pick up his prefabricated wood silo house," says Gurney.
He notes that about two-thirds of the sales have been complete new silo houses, with the rest being additions to existing homes. Some have been built by do-it-yourselfers, some by contractors. Size has ranged from 8 to 36 ft. in dia., and up to about 40 ft. tall.
Unadilla sells a pre-fabricated silo house package complete with instructions, to build the outer shell and roof. There is no standard model or design.
Here, according to Gurney are key features of Unadilla's Silo House pre-fabbed package:
"Generally speaking, the 2 in. tongue and grooved material we furnish is untreated Eastern Spruce silo staves. We provide a single or double wall cylinder of any diameter or height, and sufficient steel hoops to go around them to assure tight vertical joints. We can make provisions in the hooping to allow for doors or windows at desired locations. For multiple story structures, we can furnish interior wooden nailing rings with supporting angle irons to facilitate installation of additional floors. If desired, we can supply a tread and riser design for a circular staircase, either inside or outside, along with supporting angle irons. Our present conical or gambrel roofs will fit even diameters up to 30 ft.
"The most common foundation is a poured concrete ring extending to below the frost line. Cellars or basements present no special problems.
"Although some customers have made and installed their own doors and windows, most have used a standard product, such as Anderson windows, available from local building materials suppliers.
"The majority of silo houses have been built using no additional insulation. However, with increasing emphasis on energy conservation, you might want to consider doing so. Some builders use a double wall with insulation sandwiched between the walls. Others have used interior studs, insulating batts, and an interior wall covering.
"There are exceptions but the normal procedure is to build the solid wooden cylinder first and cut in the doors and windows after it is completed. In most cases, this has been done by the purchaser, or by a local builder of his choice. Farm silo erectors are available in some areas to put up the shell if this is desired."
Gurney notes that some owners of silo homes started out by tearing down an old, weather-worn wood silo, then rebuilding it into a house at a new site. "If an old wood silo is still structurally sound, all the buyer needs to buy from us is the hoops and other hardware," Gurney points out.
The first floor in a typical silo house is partitioned into pie-shaped areas for kitchen, half bath and dining-living areas. A spiral staircase leads to the second floor and the bedrooms, or a bedroom and a living or family room, and a bath.
For more details, contact: FARM SHOW Followup, Unadilla Silo Co., Unadilla, N.Y. 13849 (ph. 607 369-9341).
To read the rest of this story, download this issue below or click
here to register with your account number.